Make New Anodes: Part of Your Haul Out Checklist
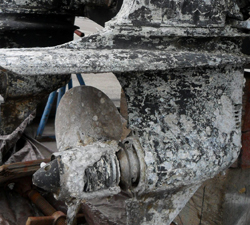
THE LOWLY ANODE IS ALMOST CERTAINLY THE MOST OVERLOOKED AND NEGLECTED COMPONENT ON MANY BOATS -AT LEAST UNTIL CORROSION STARTS EATING AWAY EXPENSIVE PARTS LIKE DRIVES, SHAFTS AND PROPS.
When it comes time to haul out this year, plan to give all your underwater gear a close inspection, measure and replace your anodes now and know you are ready for next season. In the fall, you can do this at your leisure. Understandably, we seem to be in a rush to launch again each spring and once the boat is in the water, replacing anodes is difficult to say the least!
Anodes are available in three different metals; zinc, aluminum and magnesium. These days, we try to make environmentally friendly choices. Boat owners seeking a “greener” sacrificial anode have an option that works better than the old, familiar zinc versions while costing less: aluminum anodes.
Aluminum is a far better environmental anode choice than zinc. Though zinc is a heavy metal—not particularly desirable to have in excess quantities in water—the big concern is with the percentage of cadmium that zinc anodes must contain in order to work as anodes.
Cadmium is a nasty heavy metal, with its use and disposal becoming increasingly restricted and regulated. In anodes, it’s of considerable concern to scientists studying estuarial pollution and its inevitable presence in aquatic life, especially once in the human food chain.
Fortunately, boat owners already have a safe and cost-effective alternative in aluminum anodes.
Leading commercial vessel operators have used aluminum anodes for years. Propulsion system manufacturers such as Mercury Marine standardize aluminum anodes to protect their marine engines, as well as specify them as OEM replacement parts.
So why do boaters still cling to zincs? Old habits die hard, and most people don’t pay anodes much thought, let alone understand how they work. An anode’s purpose is to protect expensive metal components from galvanic corrosion. The simple science is that when a boat is in the water, its various metal components are exposed to galvanic corrosion, though not all corrode at the same rate. Those that corrode fastest are “least noble,” while the “most noble” corrode most slowly.
This is why relatively low cost, replaceable sacrificial anodes are made from less noble metals. The inexpensive anode is sacrificed, rather than the costly propeller shaft, engine, rudder, engine cooling system, refrigeration condenser, or even the hull.
While anodes may appear to be fairly inert pieces of metal, they are actually sophisticated pieces of anti-corrosion engineering. Their complexity lies in that they are truly alloys, made to an exacting specification in order to sacrifice effectively, but at a controlled rate. Aluminum anodes, for example, contain trace amounts of indium and other components to help them perform properly.
The U.S. Navy has done very extensive work on determining the alloys, composition and, importantly, the production process to create effective sacrificial anodes. Consequently, the Navy’s MILSPEC for anodes has become “the global benchmark for shipyards and ship owners,” says John Mitchell, president of leading anode manufacturer CMP Global, headquartered in Vancouver, B.C.
Anodes that wander too far from the specifications won’t work, as various forms of surface oxidation will slow, or even halt, the sacrificial process. Be careful when inspecting your own anodes – if they don’t seem to be sacrificing, other metals may be!
Apart from having the right composition for optimal protection, water salinity will affect the rate at which the anode sacrifices, and its overall effectiveness. In salt or brackish water, the anode material will be zinc or aluminum. While aluminum is superior across a greater range of salinities than zinc, the recommendation for vessels that operate only in fresh water is magnesium.
For our readers on inland fresh-water lakes or the Great Lakes, magnesium is the right choice. If the boat is going back and forth from fresh water to salt, aluminum seems to be the only answer. Aluminum does lose its effectiveness in fresh water but will begin working again once the boat enters salt water.
To provide better fresh water protection, a supplemental magnesium anode called a ‘grouper’ can be hung over the side of the boat.”
But what about the cost of aluminum anodes, since it’s a more expensive material than zinc? The rate at which an anode sacrifices is controlled by the surface area it presents to the water, and equivalent aluminum and zinc anodes will have the same dimensions. While pound for pound aluminum costs more than zinc, an aluminum anode will weigh less than half of its zinc counterpart and should therefore cost less.
The big payoff though, is that aluminum anodes have a longer effective life. Cathodic protection specialist Paul Fleury, an ex-U.S. Navy nuclear plant technician and founder of Marine Services in Earlysville, Virginia, says that in terms of protective power, aluminum anodes have 3.5 times the energy of zinc anodes. They also have 20% better self-cleaning benefits, in his experience.
When choosing replacement anodes, ask the chandlery or marina for the Navy’s MILSPEC benchmark. The market contains many inexpensive anodes but most live up to the saying, “you get what you pay for.”
For more information contact: www.canmet.com
Photo caption: A badly corroded stern drive needing major parts replacements. This should never have gotten this far – white blemishes advancing that far indicates lack of anode protection. Don’t forget that each engine and drive manufacturer specifies internal anodes that need periodic replacement as well. Replacement anode kits for all major manufacturers are now available in aluminum