Fuel Filtration – Once Again, For the Record
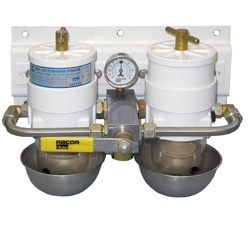
By Robert Buller
There is no end of discussion and debate about the fuel filtration needs of diesel engines. Myths and half-truths abound. So let’s set the record straight.
Diesel engines are the most reliable of all internal combustion engines; they are robust and they need only two simple inputs, air and fuel. Properly maintained they will perform well for upwards of 15,000 hours before needing a re-build. By contrast, that is about three times the life of a well-maintained gasoline engine. Diesel fuel is usually cheaper than gas and diesels of a similar size will outperform their gas counterparts with more distance covered per unit of fuel used, whether it’s a truck, automobile, or a boat.
Diesel engines ask little of their owners. Start by keeping the oil clean by changing it and the filters every 150-200 hours, or annually, whichever comes first. More importantly, filter the fuel so it is clean too. Diesel engines need a much cleaner fuel than gas engines simply because the tolerances for a diesel fuel injection system are so fine that contaminants in fuel can stop a diesel cold and may even necessitate a very expensive repair. Dirty fuel is a reality these days, no matter where you purchase it. So what to do?
Diesel fuel is a complex mix of over a dozen hydrocarbon molecules and it is formulated specifically to be self-lubricating; it’s slippery to the touch, and to the fuel system of the engine. It will ignite with only compression pressure, whereas gas engines need a spark to ignite. But diesel fuel will also oxidize and get “stale” over time and in the presence of air. With time, the diesel hydrocarbons change shape and character (this is called polymerization), and this process starts within a month from the refinery.
These changes can make diesel fuel more difficult to burn and can become a heavy sludge that can seriously damage the fuel delivery system. Diesel fuel should never be kept longer than two years. A stabilization additive is commonly recommended for fuel that will be kept over a period of time. Additive effectiveness can be debated but they don’t seem to do any damage and many boaters and mechanics swear by them.
Water is the most common and most dangerous fuel contaminant. Too much water can actually stop a diesel engine. But, some water will be in the fuel as a result of the refining process. The secret is to keep out any additional water. Condensation is the most common way that additional water gets into fuel. Water will actually condense on the interior walls of the fuel tank, rolling down and into the fuel. As water is heavier than fuel it will collect at the lowest point of the tank and will soon cause trouble.
Water can cause corrosion and it will also support the growth of microbes and bacteria. The warm temperature of most engine rooms will accelerate that growth and within days, millions of very small organisms are thriving in the water in the tank. Contrary to common lore, no algae can grow within a fuel tank as algae needs light to survive and tanks are dark. But, bacteria can multiply quickly adding to the sludge on the tank bottom.
This sludge might not cause any trouble if it is not disturbed. But, add a rough sea and a heaving boat and sludge will soon get mixed up and then a filter system is critical. Fuel filtration between tank and engine is a must, and it is never sufficient to use only the filters on the engine itself. That’s OK for the oil system but it is not enough filtration for diesel fuel.
How big a contaminant should we worry about?
In this field we measure tolerances in microns (see sidebar). Fuel from the refinery has usually been filtered to 30 microns, but additional contamination might occur in the transportation and retail distribution systems. For that reason manufacturers recommend a multi-stage filtration system with at least one coarse filter followed by a finer one. Dirty fuel may have particles as large as 20 microns but the dangerous ones are usually smaller than 10 microns.
Newer diesel engines put even more demands on filtration because the fuel system pressure is dramatically higher in common-rail injection systems. Upward of 30,000 psi is common today and demands very clean fuel. Even small contaminants can do damage at these pressures.
The primary filter is the one closest to the fuel tank and it should be a coarse filter of either a 30 or a 10-micron size depending on the manufacturer’s recommendations. The secondary filter is closest to, or mounted right on the engine. This filter MUST be as specified by the manufacturer. These secondary filters range between two and seven microns. The most common combination seems to be a 10-micron primary filter, followed by a 2-micron secondary filter.
Why so small? Research on engine failures showed that the most common dangerous contaminants were five to ten microns, so a 2-micron filter is sufficient. Engine manufacturers require a filter efficiency of blocking 95% of particles three microns or larger and a two micron secondary filter achieves that standard. It is also the smallest filter size that is readily available. There are 0.5-micron filters available for water purification but these are not appropriate for fuel.
Fuel filters should be changed when fuel pressure increases to a level only as high as recommended by the manufacturer. But regardless of pressure readings, filters should be changed every 500 hours or every 12 months, whichever is earlier. For seasonal boaters who do 200 hours or fewer per season, change both oil and fuel filters every year. It’s probably the cheapest maintenance investment that boaters can make.
Changing filters has its own challenges though, as it is easy to introduce air into the fuel system when changing filters, and this necessitates a bleed process. For that reason my boat was plumbed with two sets of both primary and secondary filters so that a new set was always available and was in-line. A simple t-bar ball valve makes changing to new filters almost instantaneous. This is most valuable when contaminants and sludge are kicked up when the boat is in rough waters. Storms do not create good environments in which to change filters, hence the twin on-line system.
What is a fuel polishing syatem?
Fuel polishing systems are the ultimate in fuel filtration. These add-on systems actually circulate and filter the fuel in the main tanks, all the time that the main engines are operating, or on the owner’s instructions. Fuel polishing systems include a separate pump, filter set and controls that can circulate the main supply of fuel and continuously filter out impurities. So, they pump continuously while the engines are running, or can be run independently from battery or shore power whenever the owner wishes. Polishing adds significant fuel cleaning capabilities.
Dirty fuel may be a given these days but a well-designed fuel filtration system will go a long way to make diesel engines as reliable as they are intended to be.
A micron is one millionth of a metre, or one thousandth’s of a millimetre. It is the small unit measurement of the metric system and it has surpassed the more common SAE unit of a thousandth of an inch. A micron gives a more precise measurement of very small items. One thousandth of an inch, “one thou” in common parlance, is actually 25.4 microns.
For comparison, a grain of salt is about 100 microns and a human hair is between 50 and 90 microns. A particle of about 40 microns can be seen with simple magnification. A single bacterium is about two to four microns. It is possible to filter out all dangerous bacteria and thus actually sterilize water with a 0.5-micron filter. For fuel, though, the concern is contaminants between about five and ten microns and a 2-micron filter is the finest that is commonly used. It will achieve a performance of blocking 95% of contaminants three micron or larger, the standard recommended by industry experts.
Photo Captions
Photo 1 – In this dual-element system from Racor, only one filter is used at one time. The controlling valve handle selects left or right, while the vacuum gauge indicates when flow is restricted and the filter element needs replacing.
Photo 2 – A secondary filtration mount and replacement filter canister. This unit is typically mounted on the engine just upstream of the injector system.
Photo 3 – Typical accordion-folded paper filter replacement elements in various sizes for Parker Racor systems – inexpensive and possibly the best engine maintenance dollars you can spend.
Photo 4 – This 10-micron filter unit combines a metal replacement canister with a visual inspection cup for the removal of contaminants. These are commonly found on smaller auxiliary engines and gensets.