Ask Andrew: A Hose is not just a hose – Part 1
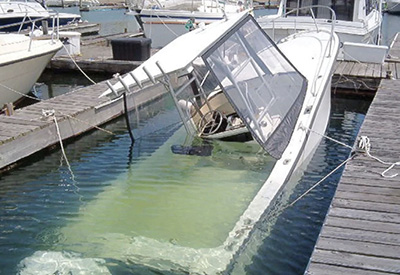
July 22, 2021
the possible result in damage to below-the-waterline hoses
I have more than once heard it said (from a cost-conscious boater), that products that have the word ‘marine’ printed on the label, is excuse for doubling the price for the same item purchased for non-marine use.
BUT there’s a reason that some products are used in certain instances. I can think of nowhere on a boat that this is more confusing than hoses.
There are so many applications for hoses aboard, and each requires a specific type. There hoses for: fuel, exhaust, scuppers, engine water intake, potable water (hot and cold), waste, water heaters, bilge water, gear lube, and blowers.
The American Boat and Yacht Council (ABYC) sets standards for boating safety – if you’ve had a boat survey done recently, you may note that many of the recommended items are according to ABYC standards. ABYC has set standards on many of these hose types, in an effort to keep boats seaworthy, and boaters safe.
a rated A1 fuel hose
Here are a few examples of why ‘marine grade’ and ‘ABYC compliant’ are important:
A client asked me to service a fuel leak. Without any more information or pictures to reference, I assumed that perhaps a fitting had to be tightened, or there was a chafed or broken line. It turns out that there was a garden hose running between the engine’s fuel pump and carburetor. The gasoline had eaten through the garden hose, causing a leak.
Another owner gave his boat a thorough spring-cleaning, and was concerned about mildew and dirt covering his hoses. He removed each one and cleaned them with acetone. The scupper hoses deteriorated due to contact with acetone, causing the boat to take significant amounts of water.
Another boater’s raw water strainer became blocked, and the blockage caused the engine’s pump to create a vacuum in the hose and the hose collapsed. Seawater poured into the boat as the engine simultaneously overheated.
Add to these stories other examples of carbon monoxide leaking through sub-standard exhaust hoses. Fuel eating through the liner of cheap fuel hoses, causing expensive blockages in the engine. Potable water lines bursting (or melting).
Here is Part 1 of a breakdown of the standards for each hose type, and the reason why the standard is so important:
Fuel Lines:
Fuel hose construction is based upon fire resistance and permeability – highly important for applications aboard, especially with gasoline.
Fire resistance is determined by the “two-and-a-half-minute burn test,” of which there are two levels. Hoses that pass the more stringent test are classified as Type A; hoses with slightly less fire resistance are classified as Type B.
There are also two types of permeability test, based on the migration of gas vapour through the walls of the hose. Hoses that pass the more demanding test are Class 1. Hoses that have a higher permeation rate are Class 2
Because of this, we end up with 4 classes of hoses: USCG Type Al, USCG Type A2, USCG Type B1, and USCG Type B2. To qualify for any of these categories, the hose designation, date of manufacture; and the name of the manufacturer (or a registered trademark) must be written on the hose. Otherwise, it is not legal in those systems-primarily inboard gasoline engines, and inboard/outboards that must comply with these regulations.
The regulations state that for inboard gasoline engines and inboard/outboards, any hose run as a fuel line between the fuel pump and the carburetor must be classified as Type Al. (Type B1 may be used on systems with anti-siphon valves). Vent and fill lines must be type A1 or A2
ABYC H24, Gasoline Fuel Systems requires Type A2 hose on all fill hoses inside engine compartments. It also covers outboard motors (requiring B1 or better hoses). ABYC H33, Diesel Fuel Systems extends similar standards to inboard diesel engines, and includes a modification that allows any of the four classes of hose to be used for fill and vent hoses.
Further than hose construction, these standards also specify maximum acceptable tolerances between fuel-line hoses and any nipples to which they are attached; require a bead, flare, or serration on the nipple (but do not allow installation of hose over a pipe thread); and require a hose clamp that does not “depend solely on the spring tension of the clamp for compressive force”
Double clamps are required on fuel-fill pipes, each with a minimum band width of 1/2″ ABYC requires the clamp to be “beyond the flare or bead, or fully on serration where provided, and at least 1/4″ (6mm) from the end of the hose”.
Fill pipes are required to have a minimum 1 1/2″ inside diameter; vent pipes a minimum 9/16″ inside diameter. ABYC states that they must be self-draining (not normally full of fuel)
Exhaust Hose:
a reinforced exhaust hose, double-clamped – preventing water and fumes from escaping
Exhaust hose requires a heavy-duty, fabric-reinforced construction. Until the early 2000’s there were no standards governing these hoses – but the Society of Automotive Engineers- (SAE) changed this requirement through their standard for marine exhaust hose, SAEJ2OO6. This standard was adopted by ABYC, and requires that the hose be able to withstand a total loss of cooling water for two minutes with the engine running at full power, and still not suffer a loss of integrity.
Exhaust hose comes with or without wire reinforcement – known as ‘hard-wall’ or ‘soft wall’. Hoses that are longer than 4-6 times the inside diameter of the hose, or with tight curves are wire reinforced for added support – this prevents the hose from chinking on bends, sagging on long horizontal runs, and pulsing from the constant pressure changes that occur in an exhaust.
Sometimes a soft wall hose is preferred: The wire in hard wall hoses can rust if exposed to atmosphere, weakening the hose. In rare cases, the wire can also be a path for stray galvanic current, or short circuits. In a more common and practical sense: the wire is tough to cut, leaves a sharp edge, and the wire can make it tough to get a tight seal where the hose is clamped.
Exhaust hose–particularly the soft-wall variety–should never span open spaces or be hung from deck beams, because panting will cause chafe at the supports or hangers.
ABYC P1, Installation of Exhaust Systems for Propulsion and Auxiliary Engines, calls for double-clamping all exhaust hose connections, with a minimum band width (for each clamp) of 1/2″: in order to minimize the chances of carbon monoxide and water leaks into the boat.
Next time (August 12), a look at Ra-water hose, fresh water hose and more….
Andrew McDonald is the owner of Lakeside Marine Services – a boat repair/maintenance firm based in Toronto. Andrew has worked in the marine industry for 12 years and is a graduate of the Georgian College ‘Mechanical Techniques – Marine Engine Mechanic’ program.
Questions or comments for Andrew? Email him directly via: askandrew@lakesidemarineservices.ca