CYOB Inbox: October 28, 2021
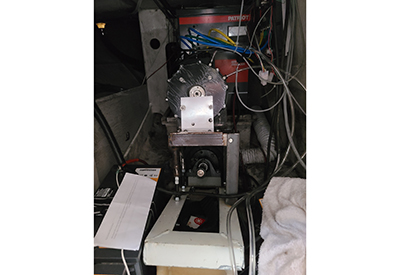
Octy 28, 2021
David/ Jackie
Congratulations on successfully navigating your boat into Georgian Bay. (see Nav, the old school way, Sept 23 CYOB)
I’m a Past Commander of Richmond Squadron and have taught boating for CPS for 20 + years. I suggest to you that all electronic navigational instruments, including GPS, are not our enemies.
On the contrary, safe boaters should be aware and utilize them with knowledge and understand. Ignoring them as we go forward is not acceptable and wise boaters utilize them practically and with good common sense.
We must always recognize newer modalities that will make boating better and safer.
With my best wishes
Larry Gaum. JN
Electric Conversion report
Hi John,
We emailed earlier this year. I have gone the first season with flawless operation of my conversion. If I had a do over, it would have been to do it sooner. Range is my downfall, but with better batteries, this will be increased substantially. I have the pictures on my phone. I can email you if you’re still interested in my story.
Cheers
Charlie Boudreau
Who can resist an offer like that!
Hi John,
Once I had cut the engine mounts out of the boat, I was all in. The next step was to smooth the inside of the hull out. Measuring the prop shaft angle to the hull angle (17 degrees), I could cut the bearing mounts out of 1” plywood pre-fitting the mount before I had to lay wetted fiberglass where the bearing mounts were going. It would have been easier if I had moved that part forward (away from the stuffing box) another inch to give me more room for the driven sheave (see photo ) and the hull. Realizing the packing gland (stuffing box) would leak, I made sure aft part of the bearing mount wouldn’t catch the water and rot the mount. I built it low knowing I could shim the bearing later for alignment purposes. Once dry, I was able to lag the steel bearing mount in to the wooden mount.
The motor I chose is equivalent to 22 horsepower and spins up to 6000 rpm (this can be digitally controlled but torque would drop). The engine I had removed maxed out at 1600 rpm so the synchronous belt (used versus a v belt in case it got wet) and sheaves had to match. I figured a 2.5 to 1 ratio therefore I have a 21 tooth synchronous sheave on the motor and a 48 tooth on the propeller shaft. The original shaft was short and didn’t allow for the diameter of the driven sheave so I had to cut another shaft out of 1″ 316 stainless. After that, cutting the shaft, threading it to match the taper on the propeller and cutting the keyways. I chose to switch to a feathering because if the unit is on and in reverse, it is supposed to regenerate power back into the batteries (4 12 volt AGM’s in series) although I’ve reached 7.2 knots and it hasn’t worked yet. I wouldn’t have invested in this and just stuck to the folding prop.
This is a picture of the outboard bearing and motor suspended to the frame I welded. I wasn’t sure if there would be any play and left enough room for 2 identical bearings. Behind that is a 48-volt battery charger for a forklift. 20-amp shore power runs this. I would have used a golf cart charger instead (a little slower, but won’t trip out a 120 volt 15 amp circuit). Word of caution, don’t leave unattended as it will produce explosive gas and heat (I use the blower).
All in all, the motor is mounted above the propeller shaft. It will adjust to tension and change belts. The system is 48 volts made up of 4 12-volt AGM batteries in series circuit. Being AGM’s, the depth of discharge is 50 % of the 100-amp hour capacity. I intend to replace them with LIFEPO4 batteries once they’ve passed. This is all fed by 4 75-watt solar panels to a 48-volt charge controller that is in parallel with my house 2 12-volt AGM batteries. My range is 1 hour at full speed. The solar will charge the batteries to 54 volts and supply a full charge in 2 days. The motor and controller were purchased through Golden Motor in Bolton Ontario. Although the system isn’t quite plug and play, they are very good at service after sales. I recommend buying both at the same time with the computer cord. I also recommend a water-cooled motor (separate pump is required). Coming into the Kincardine Marina under power, the motor overheated (no damage, there is a sensor in the motor so it cuts out at specific temperatures) and stopped working because the coolant was dry. This was the last time the motor went without water and it has worked flawlessly since.
Using the same stuffing box and new graphite packing, the 1″ shaft should be buffed in this area as well as the cutlass bearing. Inclinometer measurements were taken from an app on my cell from the inside of the boat’s hull to the shaft in the center of the stuffing box. I chose a pillow block bearing with 2 locking screws for alignment purposes that can be lubricated with a grease gun. Don’t use the collar type as it will undo in forward or reverse!
Sheaves and belts were bought over the phone from Toronto Bearings. Their help was friendly and professional.
Costs:
Motor $1500
Controller $1100
Belts and sheaves $600
New shaft (I bought 316 1” round bar and machined it myself) $200
Fiberglass $200
Weight loss:
Engine 400 lbs
Engine mounts 150 lbs
Gas tank and gasoline 250 lbs
Weight gain:
Batteries 440 lbs
Motor and controller 50 lbs
Battery charger 150 lbs
Cheers,
Charlie