Ask Andrew: Understanding Sealants
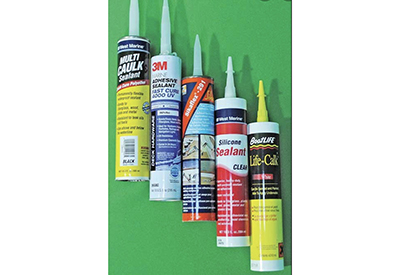
Feb 27, 2020
a selection of popular marine sealants
Over the winter, a many-thousand pound fiberglass, wood or metal shell is held in position by only a few plywood pads, or perhaps by two trailer bunks. In the spring, many of our boats are lifted by two slings into the water, putting enormous pressure on the sides of the hull, causing it to flex and shift. While in the water, the pounding of waves, straining of rigging, driving rain and UV exposure are the norm. It always amazes me how boats hold up under the abuse that we put them through.
To exacerbate the problems above, we’ve created boats about of many types of materials that have to work in concert, together: steel is bedded to wood and fiberglass, rigid porthole frames are set into flexible cabintops, plastic bushings and through-hulls are used extensively, bronze and copper are set at right angles to wood grain – and this is on top of the flexing, twisting and pushing forces that constantly work on a boat. Boat builders, shipwrights, marine techs and owners reconcile all of these contradictory actions in a number of ways – but one of the most overlooked and undervalued is the correct use of sealants. (Note: I’ll use the generic term ‘sealant’ in this article to describe the material used for bedding, bonding and sealing. Another common term is ‘caulking’, which I also tend to use interchangeably).
Hundreds of years ago, gaps in planking aboard wooden clippers were filled using cotton, hemp and tar. Over the years, we’ve made great strides in understanding how wood shrink and expands, and the best methods in compensating for these changes. The era of fiberglass, carbon fibre and Kevlar has seen a number of chemical sealants which are becoming more and more sophisticated and specialized. With the number of options available on the market, how do you decide which to use, and when?
The use of these products is based on a few factors:
The purpose of the repair: Are you bedding, sealing or bonding?
The location of the repair: is it above or below the water line? Is it in a wet or dry area?
The nature of the repair: should the sealant remain flexible, or are rigidity and strength required?
Selection charts and MSDS sheets are the best way to select the right sealant for the job.
Different jobs require different sealants. Lets define a few of these terms:
Bedding: the process that seals water out when installing hardware. Any time a screw or bolt goes into wood or fiberglass, it should be bedded using a sealant.
Sealing: similar to bedding, it is the layer between two parts. The seal may be flexible or rigid. This is done around hatches and portholes, but also around through-hull fittings and deck hardware. The use of a gasket material is also ‘sealing’
Bonding: adhering two parts together: gluing. Often rigidity and strength are called for.
When bedding hardware (such as putting a screw into wood or fiberglass) the purpose is two-fold: First and foremost is to prevent the intrusion of water, rotting the core of the material that the screw is entering. Secondly, it provides a buffer between the two materials as they flex and move at different rates (think of stainless steel deck hardware against fiberglass – the fiberglass will flex much more than the stainless steel).
Bedding compounds like 3M 5200, 4200, Sikaflex 291 and 292 are good choices
Sealing comes in two types: above or below the water line. Sealing is necessary in areas where solid hardware isn’t necessarily used – when installing a through-hull, or a hull-to-deck joint, or between the planks of a wooden boat. Sealing is also done around portholes and hatches.
Sealants like 3M 5200, 4200, Sikaflex 291 and 292 are great for underwater usage. For above the water (on decks) marine-grade silicone products like Butyl tape, 3M Silicone and Boatlife Life Caulk. If an epoxy is needed to combine the benefits of both bonding and sealing, West System’s G-Flex is an option
Bonding can be done above or below the waterline for scarf joints, permanently securing hardware, or as a permanent adhesive. Products like Wood glue, JB Weld, and two-part thickened epoxies (like West System’s Six10) are good choices depending on the application.
Other factors that will affect your choice of sealant are: ease of application and clean-up, price, the flexibility of the cured sealant, and its ability to be taken apart or repaired (3M 5200, as an example, is an excellent sealant both below and above the waterline, but is very difficult to remove once applied). Other factors such as colour availability, cure time, ultimate strength and price.
the work area taped off before laying down a bead of sealant during a hatch installation
In terms of application and use, here’s a few tips and tricks to make the job easier:
When sealing around exposed edges, tape is your friend. Use painter’s tape to edge off the areas that you DON’T want the sealant to end up on, but make sure to leave enough of a layer or edge for the sealant to do it’s job.
Press the sealant in place – don’t rely on a surface layer – use a rounded tool or a gloved-finger to press the sealant in any joints, spaces or gaps.
Keep nitrile gloves, garbage bags, acetone and rags handy for clean-up. I find that acetone works very well in removing caulking from fiberglass and gelcoat surfaces. Sealants tend to get into the grain of woods and can be quite difficult to remove – so cover these areas with paper and tape while working. Finally – sealants get everywhere – on clothing and skin. Wear clothes that can get messy, and cover your skin to avoid the mess.
Andrew McDonald is the owner of Lakeside Marine Services – a boat repair/maintenance firm based in Toronto. Andrew has worked in the marine industry for 12 years and is a graduate of the Georgian College ‘Mechanical Techniques – Marine Engine Mechanic’ program.
Questions or comments for Andrew? Email him directly via: askandrew@lakesidemarineservices.ca