Your propeller – The Unsung Hero of Boating
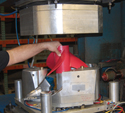
Doesn’t a propeller look simple? Visually, the size and shape makes it obvious that a propeller kind of “screws” its way through the water and to a casual observer, it looks to be one of the simplest parts on the whole boat.
Well, it’s exactly the opposite. Your propeller is the unsung hero of boating. It’s probably the single most complex piece of engineering on the boat. The size and shape of the blades and their angle to the hub are just the start of the story. The thickness of the blades, the rake and angle of attack at various points along its length, the finishing of the blade edge, whether or not it has any “cup”. These are all factors and there are many more.
Change just one and the performance changes.
Two miles per hour; that’s what we lost when we accidentally backed out a little too far and at idle speed in gear; our prop blades just kissed the edge of a rock. After that, the GPS revealed that the boat was running 35.7, not the previous 38 mph. We still got the maximum revs too…just not the speed.
We put the boat on the trailer and looked at the propeller. At first glance, the prop looked to be OK. Expert examination showed that it was out of “index”. Index is the space between the blades. Our almost unnoticeable accident could also have put the prop out of “track”. Track is the relative height of each point. Sometimes a propeller strike bends all blades equally. The GPS does not lie though. We immediately lost 2 mph off the top speed.
Even minor prop damage can set up a noticeable vibration at various speeds that can cause future damage to gears, seals and drive train parts. Of course, performance and fuel economy can suffer too!
Luckily, there’s a great solution to this and it’s cheap – sometimes even free and you can do it this winter when your boat is in storage.
This winter is the perfect opportunity for you or your marina to remove your prop and have it checked out. Often, there’s only a nominal charge for a prop check that could reveal damage that could be costing you lost speed, wasted fuel, or excess engine vibration.
Many props can be “tuned” or repaired for minor damage, being out of index, or out of track. If a blade is nicked, bent or cracked, it may be possible to repair it and if the prop is badly damaged, you should just replace it anyway.
Props are not inexpensive (although repairs are quite affordable) because they are actually quite tricky to make. They are even harder to design but that’s for another article!
We recently traveled to Fond du Lac, Wisconsin where we had the genuine pleasure of touring the Mercury Marine propeller plant to watch their experts cast and machine new stainless steel propellers. The following photographic tour will give you some appreciation of the effort it takes to make a new propeller.
Incredibly, Mercury has over 500 different wax patterns for propellers. They make a die cast wax pattern in a special wax formulation that later gets recycled. The wax pattern is coated in colloidal silica sand and slurry of binders like a milkshake to build the ceramic up to five layers.
The ceramic shell is the “investment” in investment casting. The technique goes back to 4000 B.C. While aluminum can be cast in a metal die (making it less expensive), molten stainless steel at 3,000° would simply weld itself to any kind of metal die. Only a ceramic shell can take the heat and later, it has to be smashed off the part.
The ceramic shells dry in temperature and humidity controlled rooms before going to an autoclave that removes the wax. Next, the now empty ceramic shell goes to a “burn-out” furnace that heats it to 2,000° F to reduce thermal shock in the “pour”, burning out any remaining wax and strengthening the shell.
An induction furnace melts the special Mercury X7 alloy at 3,000°. In a separate oven, the ceramic shells are heated more before being placed on a cart near a special overhead robotic arm. The operator uses that to manipulate with the ladle of molten stainless steel, pouring it carefully and with precision into each ceramic shell.
Once cooled down, the ceramic shell is broken off leaving a dull gray propeller. It then goes to a highly skilled technician who balances and machines the prop before final polishing. His work is more like art than manufacturing.
These little Tetrahedron shapes are called “cut media”. They are polyester resin with aluminum oxide grit. It’s curious that they wear evenly in the huge polishing bin as the propellers slowly rotate. Twenty pounds of cut media is used to polish one propeller at $1.85 a pound!
The final step is another polishing process using porcelain pellets with aluminum oxide for the final polish. We’ve skipped over dozens of important details but these are the main steps your new stainless steel prop goes through to be manufactured.
As probably the number one propeller manufacturer on the planet, it still takes Mercury five full days from wax pattern to a boxed product ready to ship!