Reducing Engine Noise
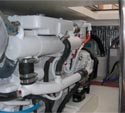
A quiet boat is a good boat. “Quiet” says well engineered, solidly built, comfortable to ride in…new. New boats are quiet. Old ones are noisy – power or sail. Why is that? In a recent technical presentation, we learned that the life expectancy of the sound absorbing materials in most new boats is about 10 years.
It turns out that the material breaks down, packs down and generally looses effectiveness as the years go by through moisture absorption and other deterioration.
Making matters worse, the many sources of vibration and impact that every boat suffers when underway, will loosen almost any bolt or fastening eventually. Things start to rattle and squeak and with the diminished effectiveness of your sound insulation materials, the boat gets louder and louder every year.
Now the good news: you can fix much of this yourself over this winter.
Assuming your boat is accessible, the winter is a great time to renew that solid, new feeling. Sound insulation materials are relatively inexpensive and they are readily available too. Your dealer probably has exactly what you need in their parts inventory. Otherwise your friendly marine chandlery will almost certainly have a selection of materials and related supplies.
DO NOT use any material that is not a proper certified marine grade material for use in the application you are planning. Fire and water resistance are critical. Buy the right stuff or hire your dealer or boat yard to do the work. Engine rooms can be noisy, hot and there is a potential for fire.
Start by assessing the existing material and noting where and how it is fastened in.
Because every engine has a different sound signature, we assume the builder did their research and used the best material for that sound signature. Do your best to duplicate the material. Don’t overdo it though. Going too thick is a waste and can make clearances too tight.
There are two types of sound sources:
Structure Borne Noise
Structure borne noise is mechanical vibration in a structure that can become an audible sound, like flexing of a tank side, loose parts rattling and so on.
Airborne Noise
Airborne noise is sound waves being carried by the atmosphere, like engine noise, turbo whine, water-makers and so on.
To control airborne noise, you use materials that block or absorb noise transmission while with structure borne noise, use isolation and damping.
Incidentally, the mounts for your engines and onboard mechanical devices should be maintained regularly to help isolate and damp vibrations. Engine mounts seem to be the last thing that ever gets tightened or adjusted on older boats and they can cause or solve many vibration problems.
Reflected noise can actually make an environment louder. So, if you can abate noise at the source you treat smaller areas and eliminate secondary effects.
Also, loosening a simple little engine room access plate or cover can open up a noise path. If you can see it, you can hear it. So, if your boat has had a hole or opening made in a bulkhead for new wiring or plumbing, you need to get advice on how to properly seal that noise source off.
You need to leave room for treatment when you add a mechanical device like an air conditioner or generator too. People often retrofit equipment into older boats but neglect to add appropriate sound control material.
There are three main methods to reduce sound:
Absorbers
Sound absorption will reduce the reflected sound inside an enclosure or room. When the sound waves strike a sound absorbing material, the sound wave has an energy conversion of kinetic energy to heat. Typically, sound absorbers are porous materials such as open cell foams or fibers.
By placing a face on the porous materials, (like the silver foil in the photo above) the absorption characteristics of the system will change. In addition, some absorber materials have a barrier hung in the matrix for added effectiveness.
I suspect that most people think of foam or fiber type engine room sound absorber as being “the” noise control material but there are other types to consider.
SMALL PHOTO: Absorbers – CAP: The first square is a small sample of absorber for use in engine areas. The white square is absorber to line areas in the hull reducing reverberation.
SMALL PHOTO: Headliner – CAP: These are also absorbers; the dark square is applied behind finish work while the white square is headliner for ceilings.
Barriers
Barriers work on the principle of blocking noise from passing through. The phenomenon of blocking noise is called sound transmission loss [TL] and this is normally reported in decibels [dB]. A common reference would be a noise reduction from the noise source side of the barrier (like the engine room) to the opposite side of the barrier, (such as the salon). Typically, barriers are air impervious solids. Another common characteristic of barriers is that they are flexible and relatively heavy.
SMALL PHOTO: Underlay – CAP: The thin square is barrier for blocking engine room noise while the dark square is firm foam with a barrier top used as flooring underlay.
Damping
The third principle in noise control is vibration damping. Vibrating surfaces act like a large speaker cone. They displace air which creates noise. To convert this vibration kinetic energy into heat, damping material is applied to the vibrating surfaces. The damping material is typically visco-elastic. Visco-elastic materials have the property of having a high loss modulus also known as loss factor. The higher the loss factor, the more efficient it will be in converting the vibration kinetic energy into heat. Apply damping material to the flat sides of water or fuel tanks, or to the prop wash area of the hull.
When considering adding or replacing noise control materials on your boat, remember that structure borne noise will travel along all rigid hard connections until it finds a sympathetic surface to radiate sound. So, introduce isolation barriers where practical, on bulkheads, tank surfaces and so on.
Then, airborne noise will follow any air path until it reflects off a hard surface, so make sure air paths are either sealed or take “tortuous” routes where the airborne vibration must make turns. Line as much surface area as possible with sound absorbers or absorber/barrier composites.
When in doubt, get professional advice and remember – silence is golden!