La fibre de verre est-elle recyclable? Deuxième partie – Émergence d’innovations
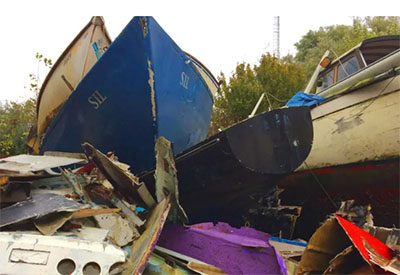
25 mai, 2021
L’intérêt de trouver des usages pour la fibre de verre usagée devient source de créativité. Par exemple, un partenariat d’universités américaines et irlandaises appelé Re-wind a permis de développer des idées de projet d’ingénierie prometteuses pour la réutilisation de pales en fibre de verre. Des pales de structures ou de tours de production d’électricité servent à des unités de logement d’urgence ou à coût modeste. En Irlande du Nord, elles pourraient servir à faire des ponts piétonniers pour des voies vertes.
D’autres options commencent à voir le jour. L’industrie de l’éolien de l’Union européenne représentée par WindEurope s’associe avec le Conseil européen de l’industrie chimique ou Cefic et l’European Composites Industry Association (EuCIA) afin de développer de nouvelles façons de réutiliser la matière des pales. Quelques 14 000 pales de turbine seront mises hors service en Europe dans les prochaines années. Le consortium a produit un rapport à cet effet en mai 2020.
Une considération majeure du recyclage des matériaux composites est de s’assurer que le processus ait un résultat positif net par rapport à leur enfouissement. L’Allemagne en offre un bon exemple. On recycle des pales de turbines pour en faire du ciment depuis une dizaine d’années dans le cadre d’un partenariat entre Geocycle et Zajons.
Comment recycle-t-on la fibre de verre?
Il existe trois procédés pour recycler la fibre de verre : le broyage, l’incinération et la pyrolyse.
Le broyage, le plus évident, consiste à découper et à le déchiqueter en petites pièces ou en faire de la poudre pour utilisation dans d’autres produits. On peut arriver à recycler ainsi à peu près tout avec très peu de perte. Ce procédé nécessite beaucoup de main d’œuvre et endommage les fibres et le produit sert de remplissage pour du ciment ou de l’asphalte, par exemple.
L’incinération ou oxydation thermique fait que le matériau sert à produire de la chaleur pour d’autres usages, comme pour créer de la vapeur pour des turbines générant de l’électricité. Ce procédé donne malheureusement un sous-produit, des cendres, qui vont le plus souvent à l’enfouissement. De plus, la fibre de verre contient peu de matière organique – entre 25 % et 30 % – et elle dégage donc peu de chaleur tout en ayant un contenu de cendres élevé.
La pyrolyse est un procédé de décomposition chimique ou de transformation du matériau en une ou plusieurs substances récupérables en le chauffant à très haute température dans un environnement appauvri en oxygène. La fibre de verre se décompose ainsi en trois substances pouvant être recyclées : du gaz pyrolytique, de l’huile pyrolytique et un sous-produit solide. Les vieux pneus d’auto sont détruits par pyrolyse (250 millions par an aux États-Unis).
Pour être traitée par pyrolyse, la fibre de verre est déchiquetée en carrés de deux pouces qui alimentent un réacteur duquel l’oxygène est extrait par vacuum. Ce réacteur est ensuite chauffé à 760 C0 (1 400 F0). Les hydrocarbures de la résine se décomposent en gaz à environ 500 C0, ce dernier étant alors séparé en gaz et en huile pyrroliques.
Le gaz pyrolytique est très propre et son contenu énergétique est semblable à celui du gaz naturel. Il peut être vendu en remplacement du gaz naturel et il alimente les brûleurs du réacteur pyrolytique, ce qui rend le système auto-suffisant. L’huile pyrolytique est semblable au pétrole lourd brut et a moins de valeur que le pétrole normal, mais elle peut être mélangée avec d’autres huiles ou être incorporée à l’asphalte.
Quelques exemples de recyclage de la fibre de verre
L’Association pour la Plaisance Eco-Responsable (APER), France
La France a été le premier pays européen à adopter un programme national pour le recyclage et le démantèlement des bateaux. L’APER est un organisme à but non lucratif créé en 2009 par la Fédération des industries nautiques et elle a établi le premier réseau de démantèlement de bateaux d’Europe.
Selon une étude de 2017 de la Commission européenne, de 1% à 2 % des plus de 6 millions de bateaux de moins de 72 pieds – ou 80 000 par an – arrivent en fin de leur vie utile. Le réseau national de France est fait de 20 entreprises côtières et de 52 sites de démantèlement. Son objectif, avec l’aide de fonds publics, est de démanteler jusqu’à 25 000 bateaux d’ici la fin de 2023.
Rhode Island Marine Trades Association – Rhode Island, États-Unis
La Rhode Island Marine Trades Association fait figure de leader avec un projet pilote de réutilisation des coques de fibre de verre auprès de cimenteries.
Les bateaux sont d’abord débarrassés des métaux non ferreux, des moteurs, de l’électronique, des réservoirs et des tissus de recouvrement qui sont acheminés des recycleurs de tels matériaux. Les coques sont découpées et réduites en morceaux pour les cimentiers.
Ultimement, l’association espère que la pratique s’étendra à tous les acteurs de l’industrie. Selon elle, ce sera davantage la conscience environnementale et l’aspect visuel négatif d’épaves dans celui-ci qui jouera en faveur de ce type de recyclage que le pur intérêt économique.
Eco-wolf – Floride, États-Unis
Eco-wolf, une petite entreprise de Floride, produit des broyeurs de fibre de verre. Wolfgang Unger est l’inventeur de recyclage et de la réincorporation de la fibre de verre et d’autres fibres naturelles. Voyant la quantité de déchets qui finissaient dans les dépotoirs dans les années 1960, ce chimiste a effectué des recherches pour broyer et réutiliser la fibre de verre et il a développé une méthode à cette fin en 1973.
En effet, il a conçu une machine capable de « récolter » ces fibres qui offrirait le meilleur résultat pour une réutilisation dans divers secteurs, comme la production de fil de pêche.
Association de l’industrie nautique du Japon
Elle a développé son propre programme de recyclage en 2005 alors que le pays faisait face à un grand nombre de bateaux de fibre de verre abandonnés illégalement. En vertu de ce programme, un réseau de 414 marinas et concessionnaires de bateaux, de 36 entreprises de démantèlement, de neuf compagnies de processus et de cinq cimenteries participent à cet effort de recyclage des vieux bateaux.
Plus de 8 000 de ces bateaux ont été recyclés depuis 2005. Les coûts de transport et de recyclage sont refilés aux propriétaires qui préfèrent choisir cette voie plutôt que celle du dépotoir beaucoup plus cher.
Zagons Logistik – Allemagne
Cette entreprise est la seule de son genre à effectuer le recyclage de pales d’éolienne à l’échelle industrielle à son usine du nord de l’Allemagne. Les pales démantelées sur le site des parcs éoliens y sont d’abord sciées selon une technologie qui a vu le jour dans l’industrie du béton et de celle des mines. Cette opération facilite le transport des pales par camion standard.
Elles sont réduites en format plus petit à l’usine pour être mises dans un broyeur conçu pour les plastiques renforcés de fibres. Une prochaine étape réduit encore plus ces morceaux alors qu’ils passent dans un broyeur rotatif qui tourne à 8 000 t/m. Enfin, un martelage permet d’obtenir des morceaux de fibre de 0,5 pouce qui sont mixés avec d’autres matières résiduelles mouillées. On s’assure ainsi que les fibres de verre s’amalgament au mix de recyclage. Il en résulte un composite que la cimenterie Holcim peut utiliser comme substitut de carburant pour remplacer la cendre de charbon et comme matière première au lieu de sable vierge lavé.
Zagons Logistik, qui fonctionne au tiers de sa capacité, utilise entre 400 et 500 tonnes de pales de turbines à recycler à chaque mois.
Plasti-Fab Washington, États-Unis
Plasti-Fab, un fabricant de composites de fibre de verre, a lancé l’intégration de fibres recyclées à ses opérations à grande échelle, réduisant ainsi ses émissions négatives et l’utilisation de matériaux non renouvelables.
L’entreprise se spécialise dans la production de fibre de verre depuis 40 ans. Elle a fait l’acquisition d’équipement spécialisé pour le recyclage à grande échelle afin de réduire l’impact environnemental de sa production.
American Fiber Green Products – Floride, États-Unis
Dans sa récente usine de Floride, sa filiale Amour Fiber Core, transforme la vieille fibre de verre en substitut du bois pour la fabrication de planches qui servent à la production de tables de pique-nique, clôtures, digues. L’entreprise s’approvisionne à partir de bateaux, d’autos, de boîtes de camion, de motomarines, de cabines de douche et d’autres produits semblables. Elle reprend de vieux bateaux, contre rémunération, à partir de divers points de service.
IsoDan Fiberglass Recycling
Isodan a mis au point une unité mobile de production sans poussière unique en son genre. L’usine mobile en question peut se charger de recycler divers matériaux composites tel que pales de turbine, bateaux mis hors service et d’autres produits de même nature.
Installée dans un conteneur maritime, l’opération de recyclage peut être transportée comme n’importe quel conteneur partout dans le monde. Une seule personne peut mener à bien l’opération pour le recyclage de panneaux de fibre de verre, du mat de verre et autres.
Global Fiberglass Solutions – Danemark
Créée en 2009 par Don Lilly et Ken Weyant, GFS s’est d’abord intéressée aux pales d’éoliennes en tant que matériel recyclable. Avec l’aide de l’Université de Washington, elle a développé un processus breveté pour le recyclage de composites en fibre de verre. Elle se spécialise maintenant dans le design et l’ingénierie à Sweetwater, Texas, où son usine peut traiter de deux à trois pales par jour, ou de deux à trois tonnes par heure de matériau pour un quart de travail de huit heures. Elle s’attend à pouvoir traiter jusqu’à huit tonnes par heure ou une pale par heure.
Il ne manquera pas de matériaux de ce type selon GFS, car les premières pales arrivent en fin de vie et les incitatifs gouvernementaux pour l’utilisation de pales plus performantes accéléreront le remplacement de celles qui existent.
GFS ne veut pas s’arrêter aux pales d’éoliennes et regarde du côté des bateaux de fibre de verre et des avions mis hors service qui ont beaucoup à offrir.
Fabriquer de nouveaux bateaux avec de la fibre de verre recyclée
Ryds Båtar un fabricant de bateaux suédois, produit environ 3 600 petits bateaux à moteur par an avec 36 modèles de 11 à 20 pieds. Il utilise donc beaucoup de fibre de verre. Il y environ six ans, avec l’aide de l’Institut suédois des composites, Ryds a commencé à développer sa production en utilisant des déchets de fabrication qui représentait environ 10 % de sa matière de fabrication. C’est ainsi qu’est né un bateau concept de 15,5 pieds fait d’environ 20% de fibre de verre recyclée.
La quantité de fibres de verre enduites de polyester projetée pour la fabrication du pont et de la coque a diminué de 50% et les couches laminées sont faites d’une mixture de polyester et de de 33% à 40% de déchets de verre venant de l’usine même. Les matériaux servant d’âme au composite – contreplaqué, Coremat, Divinycell – ont été remplacés par cette mixture. Il en résulte un composite de force égale ou supérieure et sa capacité de tenue pour la visserie est grandement améliorée.
Au final, l’avènement d’innovations visant à réutiliser des bateaux, des pales d’éoliennes ou des pièces d’avion repose sur une demande du marché suffisante pour que soient créées des installations pouvant recycler cette matière. Il faudra également un cadre réglementaire aux États-Unis pour que les pales d’éoliennes mises hors service ne finissent pas inutilisées en entreposage permanent ou à l’enfouissement.
Le futur
Bien qu’il n’y ait pas de réponse définitive pour le recyclage de bateaux en fibre de verre aux États-Unis, par exemple, la croissance de l’industrie du recyclage de la fibre de verre des éoliennes pourrait avoir des retombées pour le secteur nautique.
Dans le cadre de la problématique du recyclage des pales, on tend à se tourner sur la matière même qui est utilisée dans leur fabrication. La recherche et développement dans ce domaine examine l’utilisation de résine thermoplastique plutôt que les fibres de verre ou de carbone. Ce matériau serait plus facile à recycler à coûts moindres.
Il faut ainsi valider les processus d’utilisation d’un matériau appelé Elium® pour fabriquer des pales dans le futur. Par exemple, deux pales de 25 m ont été réalisées dans les ateliers de Plastinov / Multiplast en mars 2018 dans le cadre du projet EFFIWIND lancé en 2014 en France. Les sociétés ARKEMA et CANOE ont collaboré à la mise en œuvre des résines thermoplastiques Elium® pour adapter le procédé d’infusion à ces nouveaux matériaux. La technique de thermo soudure employée a mérité un prix de « reconnaissance spéciale » de l’organisation R&D 100 en 2020 pour son effet « perturbateur dans le marché ».
Deux approches pour une économie plus circulaire sont une plus grande communication au sein de la chaîne d’approvisionnement de l’éolien et des objectifs ambitieux. Par exemple, la société Vestas Wind Systems, un concepteur et producteur de turbines d’éoliennes, a annoncé qu’elle s’engageait à fabriquer des éoliennes « zéro déchets » d’ici 2040.
Cette entreprise projette d’y arriver en améliorant sa capacité de recyclage au cours des 20 prochaines années en travaillant étroitement avec ses partenaires de la chaîne d’approvisionnement de manière à ce que ses produits ne soient plus incinérés ou envoyés à l’enfouissement. De tels partenariats sont nécessaires afin de combler les failles de cette chaîne et rendre les systèmes de production d’énergie 100% recyclables.