Pandemic notebook: Covid-19 hands Bay Sails an unexpected project for Air Canada
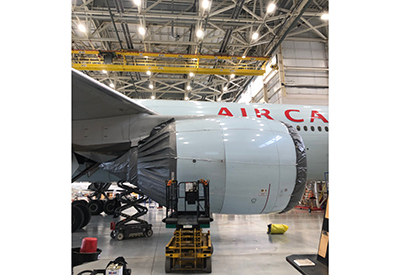
June 25, 2020
Winter is a fun time for sailmakers in Canada. We grind through mountains of repairs and have an abundance of new sails to put together and deliver. We also get to head south to race sailboats in paradise, sometimes in Florida for some Etchells, VX One or Star racing, or other times down to the Caribbean. I’ve been racing with Team Touch 2 Play for quite a few years now with owner Rob Butler of Collingwood. The last handful of years we have been doing the winter circuit of the Caribbean: starting in Grenada, touring through the islands, Sint Maarten for the Heineken, the BVI Spring Regatta, St. Thomas International Regatta, Voiles St. Barths and Antigua Sailing Week.
This year was a wee bit different. After flying home from the Heineken just as the Covid-19 outbreak made a solid landfall in Ontario, it looked like business as usual had just changed.
The first day that my kids didn’t go back to school after March break, I got an unexpected call from some aviation mechanics from Air Canada’s service hangar at Pearson (YYZ): “Can you sew big things?” they asked, “can you help us get some prototypes and specifications together?” I was officially intrigued. That afternoon Sandro Rizzi and Jairo Jimenez from Air Canada were helping me out with prototypes, and we worked late into the night to test fit a 787 Dreamliner at the hangar.
The following day we had a contract to build the first batch of seventy engine covers.
This project was similar to a sailing project: designing, test fitting, and specifying durable and appropriate materials for the purpose. Our sail loft setup was perfect! With sewing machines inset into the floor and large seaming tables to work at standing up this would suit the project perfectly.
We developed some novel approaches using custom made boltropes to secure the covers into panel gaps in the engine nacelles to fasten to, as well as highly tapered panels to snuggly fit the exhaust cones of the engines to keep out moisture and other foreign objects. Another neat detail on many of the aft covers was sewing multiple layers of fiberglass panels directly to the covers to act like large “battens” that would support the covers around some otherwise inaccessible parts of the engines.
This was a once in a lifetime project I never saw coming.
We were lucky to have a continuous supply of thread and webbing from Challenge Sailcloth in the Northeast US. We also had Brewer’s Marine on deck to provide us with hundreds of nylon hooks, 15 kilometers of polyester rope, and a few kilometers of good polyester bungee cord. We had the balance coming from all over Canada and both coasts of the US for the remaining few kilometers needed. Our friends up at Transat Western Marine in Barrie were able to help out with an emergency order of 700 more hooks that we needed. I’ve never needed so many supplies, let alone kilometers of rope and bungee cord. This was a once in a lifetime project I never saw coming.
The aircraft mechanics and engineers at Air Canada were great to work with: they are very detail-oriented and were very capable of taking full-scale patterns when required to develop new designs. Overall, we did the front and aft covers for the Boeing 787’s, 777’s, 767’s, and some of the Airbus A330’s in their fleet as well. Bonus – they can be easily installed and removed with only two mechanics and in 15 minutes or less. The crews in Vancouver, Calgary, Toronto, and Montreal airports have been pleased with the covers, and they are proudly protecting Air Canada’s planes so that they will be ready to fly when we are.
Keven Piper
Owner Bay Sails, Hamilton ON