Ask Andrew: Understanding Gelcoat
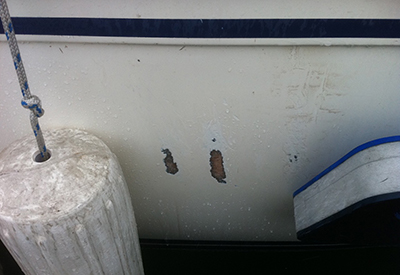
Mar 26, 2020
(Left) Damage caused by the vessel rubbing against a dock
(Right) The same area, after repair
Building on our last two editions (Sealants, and Fibreglass, respectively), Gelcoat is the next logical progression – that is, the outer part of the hull and decks. Gelcoat serves two main purposes: To protect the fiberglass beneath it, and to give a cosmetic finish as the outer layer of construction.
In the 1960s, when the mass shift began from wooden to fiberglass boat construction, boats were built almost the same way that wooden boats were, and simply sheathed in fiberglass and paint. There was little understanding of way that fiberglass could provide strength to the wooden components, and where wear would be seen years or decades later. These boats tended to be overbuilt. Modern boats, with decades of strength and destructive testing available, are able to use much lighter materials all around, with just as (or more) strength than their heavier counterparts from days-gone-by.
Because of this shift in boat building technology, Gelcoat application in modern boat production is a bit counterintuitive. Modern boats are made using female moulds: The gelcoat is sprayed 3-5mm thick into a mould in the first step. This layer is then laid up with the fiberglass, resin, and plywood/balsa supporting material on top of it. Once the hull, deck, cockpit, covers and hatch sections have had a chance to dry and harden in their individual moulds, the mould is removed, and the boat components are assembled using sealants and hardware.
Gelcoat cracking at the base of a stanchion.
It should be noted how we define Gelcoat: A gelcoat is a high-quality finish, designed to be applied on a fiberglass surface, using the same technology as polyester resins or epoxies (Ie. They don’t ‘dry’, they ‘cure’ using hardener and chemical reactions). Various colours and thicknesses of base gelcoat are available, with colour pigments available to tint and colour match. Once gelcoat is cured fully, it is a hard shell-like surface
Earlier gelcoats were made of a base white resin, with colour pigments available to match. MEKP hardener is added (as with fiberglass) to allow it to cure. Gelcoat is rolled or brushed on, and can be thinned using acetone to the desired consistency. Gelcoat can be thinned further to allow it to be sprayed on.
Spraying gelcoat on a boot stripe, using Awlgrip and an airbrush tool
A number of advancements have been made in gelcoat technology and there are a number of very high-quality brands available today: Awlgrip, Alexseal and Imron to name a few.
It should be noted that gelcoat differs from marine paint. Marine paint comes in a wide range of colour options, and many are high-quality. Marine paints tend to be slightly less durable than gelcoat, require more maintenance, but are more cost effective than gelcoat finishes (especially when looking at repairs). Interlux and Epifanes are manufacturers of high-quality marine paint.
(Left) Awlgrip (gelcoat) or Interlux (marine paint)
(Right) A Prevail sprayer – ideal for small gelcoat applications
Gelcoat is glossy and porous and is susceptible to wear and tear from oxidation, dirt and UV exposure. To combat the effects of these, polishing and waxing is recommended annually. Polishing is the process of applying a very fine abrasive (1000-2000grit) to the surface of the gelcoat in order to remove the surface layer, exposing the bright and glossy colour beneath. Professionals do this using a machine polisher and a high-grade applicating pad. This polishing action is followed by a wax application – applying a liquid wax to the surface, rubbing it into the pores of the gelcoat, and then wiping clear. On boats that haven’t been polished in a number of years, sometimes the polishing is preceded by a wet/dry sandpaper application, and a succession of grits of sandpaper and polishing compound.
Repairing gelcoat is a straightforward process on paper, but requires a bit of an artistic flair to finish it well. Gelcoat may be scraped or rubbed down against docks or lines, or may be cracked or crazed on the suface, through impact or due to the flex or tension of the fiberglass below the gelcoat, or the hardware mounted on it.
The repair process is simple enough:
1) Tape off and grind out the repair area – gelocat repairs can get messy, so marking the work area, and protecting the areas adjacent are important. Use a grinder or rotary tool (like a Dremmel tool) to grind out the damaged gelcoat, and through the depths of any cracks to the fiberglass surface.
2) Chamfer the edges of the grinding area – the other edges should be angled so that the new filling compound will adhere well to the surrounding area
3) Apply a fill/fairing compound – using a thickened polyester resin (I like to use microballoons) and I fill the repair area using a putty knife. Polyester resin’s shrink slightly as they cure – so sanding and fairing again are common.
4) Sand fair – sand the area to a fair surface, matching the surrounding area. Sand using progressively higher grit sandpaper to leave a smooth surface
5) Brush, roll or spray gelcoat – gelcoat can be rolled on using a foam or tufted roller, it can be brushed on (watch for brush marks), or it can be sprayed using an automotive-paint-style spray set-up. For smaller jobs, I like using a Preval spray applicator – it includes a small glass jar as a reservoir for thinned gelcoat, along with an aerosol-type sprayer. It can be sprayed much like spray-paint
6) Wet-sand fair – Gelcoat can take 1-2 days to cure if rolled or brushed, but can take up to 7 days when thinned and sprayed. Once cured, the surface should be wet-sanded using a very high-grit (400-2000 grit) to match the surrounding surface
7) Polish to a high gloss. The repair can now be polished and waxed
I would encourage you to attempt small repairs on your own – it’s a great way to learn the art of gelcoat repair and maintenance. If you take this on, protect the work area (spills and mistakes are likely), have acetone nearby to clean up any mistakes, and wear appropriate PPE (Face mask and nitrile gloves). Work in a well-ventilated area, and be conscious of your neighbors.
Andrew McDonald is the owner of Lakeside Marine Services – a boat repair/maintenance firm based in Toronto. Andrew has worked in the marine industry for 12 years and is a graduate of the Georgian College ‘Mechanical Techniques – Marine Engine Mechanic’ program.
Questions or comments for Andrew? Email him directly via: askandrew@lakesidemarineservices.ca