Ask Andrew: Suck Squeeze Bang Blow Pt 2 – Compression in a diesel engine
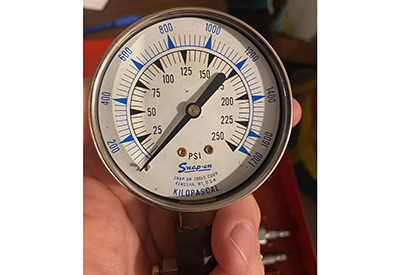
Dec 22, 2022
This is Part 2 of a two-part series on compression testing. Last edition explored how an engine works, why compression is important in engine operations, and what a compression test can reveal about the state of the engine. This week we’ll explore diesel engines, which differ from their gasoline counterparts in a number of ways.
If you spend any time around a mechanic, you might hear a couple of regularly repeated jokes designed to tease the ‘new guy’ or perhaps someone who isn’t very mechanical. One of my favorites is:
‘looks like your diesel engine might need a new set of spark plugs’
Seems obvious when it’s said out loud: Diesel engines don’t use spark plugs. But – how does the fuel ignite, then?
Let’s start with a re-cap from last edition:
Inside the engine block, a crankshaft turns to perform work: turning a prop shaft and propeller to make the boat go.
the 4 cycles of an engine: intake compression, power, exhaust
This action is dependent on the up/down movement of the pistons, contained in cylinders inside the engine block. At the top of each cylinder is a pair of valves: The intake valve allows air into the cylinder. The exhaust valve lets air out.
The fitting of the piston in the cylinder is helped by piston rings: these rings allow a tight fit, but alos provide a replaceable wear point. The movement of the tight-fitting piston is helped along with via oil lubrication.
A single piston moves up and down in a single combustion cycle. A 4-stroke engine will move have the piston move 4 times in a cycle: Intake, Compression, Power and Exhaust (Suck squeeze bang blow)
The piston moves down, and as it move, the intake valve allows air into the cylinder. The downward movement draws air into the cylinder, and when it reaches the bottom of it’s stroke, the intake valve closes.
The piston then begins to rise, with the valves closed, keeping air trapped inside and compressing it. As the air is compressed, it heats up. At the top of its stroke, atomized diesel is added, and is compressed along with the air. By compressing both, heat is generated – and when compressed enough, the diesel becomes hot enough to naturally burn. Without correct compression, this fuel won’t ignite. When temperatures are colder, or when the engine hasn’t been run, the use of glow plugs aid in ensuring that the cylinders are warm/hot enough for the diesel to efficiently ignite.
The resulting explosion forces the piston downwards, causing the crankshaft to turn and resulting in work being performed. Inside the cylinder, gases from the explosion are vented as the piston rises on its fourth stroke and the exhaust valve opens to release it.
This process happens over and over again, in multiple cylinders as long as the engine is running.
So… what could go wrong?
The engine needs three components to run – and if any of those components is missing, the engine either won’t start, or won’t continue to run:
1) Fuel – the explosion must happen for work to be performed. Without fuel available to burn, the work won’t take place
2) Heat – The right conditions must exist for the cylinders to be warm enough to allow the compressed air and fuel mixture to ignite.
3) The cylinders must have a tight seal, and be the compression is critical to allowing the diesel fuel to ignite.
Each of these three components that may be common causes of failure. Many of us have heard the term compression but may not know what it means or how to measure or fix it.
The cylinder’s compression is dependent on a few factors (not in any particular order)
a) The piston fits tightly in the cylinder. Worn piston rings can allow air to escape, preventing the pistons’ ability for it to be compressed
b) The piston is lubricated well. The wrong viscosity of oil can prevent movement of the cylinder, or might not fill the gaps between the cylinder wall and piston
c) Gaps at the top of the cylinder. A ‘cylinder head’ rests atop all of the cylinders in a row (one head may cover 1 or 2 or 4 cylinders, depending on the engine configuration). Engines are made of cast metal, and when two components are bolted together, a gasket is fitted between the two parts. Over time, with repeated compression and worn parts, the head gasket can become damaged, resulting in a ‘blown’ head gasket
d) The valves are damaged: a valve stem breaks or bends, or the valve edges become coated in carbon, resulting in a poor seal. Air escapes and compression is lost
e) The piston itself is damaged. All the explosions inside a cylinder can cause all sorts of problems over time
a compression test kit for diesel engines. Note the many adaptors to allow testing in a variety of ways.
Diagnostically – It can be tough to isolate exactly why compression is low – but we can use a simple tool to determine what the compression is in each cylinder and therefore determine what to check next.
Compression tester and test steps
The compression tester has a threaded fitting that threads in at the top of each cylinder in place of the spark plug. As the engine is turned over, the crankshaft turns, the pistons move up and down, and the air in each cylinder is compressed (without starting the engine). The level of compression (the PSI) is read via a gauge attached to the threaded fitting.
Steps.
1) Disable the engine so that it doesn’t start accidentally (if you’re unsure how to do this, consult with a qualified marine tech).
2) Mark the numbers and location of each cylinder.
3) Choose the access point for tester – compression can be tested by either removing the injectors or the glow plugs: whichever is easier to access (and whichever you have the correct adaptors for!)
4) One at a time, remove injectors/glow plugs. Connect adaptors, per manufacturer recommendations, and connect the gauge to the adaptor
5) Once set up, apply power to the start motor, or rotate the engine by hand. Allow the engine to turn multiple cycles (5-10 seconds). Read and record the results for each cylinder. Ideal cylinder compression should be between 300 and 500 psi. Note how much higher the compression needs to be in a diesel vs the 110-150psi required for a gasoline engine. Note that the decompression lever on the engine needs to be in place.
The results:
If multiple cylinders, side-by-side have low compression, the head gasket may be blown in a location between the two.
If only one cylinder has low compression, with the others reading high, the problem is isolated – meaning that the cylinder walls, piston, rings and valves in that single cylinder should be checked. The cylinders should read within about 10psi of each other.
If all cylinders are reading low compression, this would point to age and even wear: valves, gaskets and piston rings, as well as a check on the quality of oil used.
If a cylinder has high compression, there may be debris, water or build-up inside the cylinder which is creating a condition where the tester registers a higher-than-normal condition
As always, it’s important to be aware of safety measures and appropriate steps and tools to take in any sort of DIY project. If you’re unsure at any step in the process, be sure to consult a qualified marine tech for advice or assistance prior to performing a compression test.
Andrew McDonald is the owner of Lakeside Marine Services – a boat repair/maintenance firm based in Toronto. Andrew has worked in the marine industry for 12 years and is a graduate of the Georgian College ‘Mechanical Techniques – Marine Engine Mechanic’ program.
Questions or comments for Andrew? Email him directly via: askandrew@lakesidemarineservices.ca