Ask Andrew – Shrink wrap
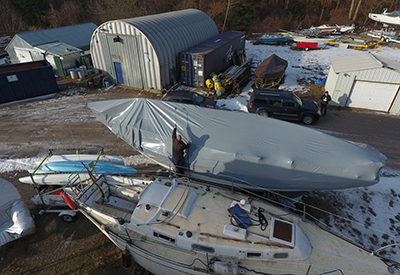
Jan 9, 2020
Heating the top sections to a tight fit
A new shrink-wrap promises more environmentally conscious
In Nov 2019, I was fortunate enough to attend the Boating Ontario conference in Niagara Falls ON. This conference is geared to members and suppliers of the marine industry particularly marina operations. One of the suppliers was Layfield Geosynthetics, offering a new shrink-wrap film called ‘Bioflex MarineShrink’. The Layfield rep that I spoke with described the new product as a more environmentally conscious option (more on what this means, below).
I was intrigued. As a marine contractor, I buy and use numerous rolls of shrink-wrap film each year at the request of my clients, who view shrink-wrap as the best option to protect their boat from the elements over the winter months. I believe that it’s a great solution for long-term storage – but I worry, as many do, about the piles and containers full of shrink-wrap to be disposed of, and how damaging to the environment this plastic might be. A new entry to the market is always exciting, but especially one that solves an identified shortcoming in the products commonly used and available.
I read some of the company literature provided, and sent an email asking for more information. After a brief exchange, we realized that in order to compare ‘apples-to-apples’, I’d need to compare how it feels, cuts, adheres and shrinks. Layfield provided a test roll (essentially an offcut of a much larger roll, cut to fit the length of boat to be wrapped) and off we went.
Draping the shrink-wrap and heating the edges
I followed the prep procedure that I’ve followed time-and again: I built a frame using 2×4’ and 1×2’s, tying in places with standard cordage. I wrapped a band of strapping around the hull, and tightened and fit all the components as I moved across the boat. Once the Layfield wrap arrived, I got to work.
The shrink-wrap was unrolled, draped and tucked. Edges were heated, cordage was added and pulled tight, and the entire wrap top was shrunk to a tight fit. Two hours later, all the work was done and we were left admiring a fairly typical job.
But there were a number of tiny touches that weren’t typical that I liked seeing:
A job well done!
1) The colour. Layfield’s Bioflex is a grey colour. The other wraps on the market come in either blue or white. The grey makes the completed job stand out in a yard full of fairly uniform boats. I also noticed, as the wrap was being heated, that the colour changed slightly as the heat was applied – it was easy to see, by noting the colour change, how much heat would be too much – giving me warning to keep my heat gun moving. It’s a subtle thing, but noticeable compared to blue and white wrap currently on the market
2) The uniformity. The current offerings in the market range in quality (and price) – these include high-quality name-brand shrink-wrap (like Dr Shrink), as well as ‘value’ brand films. The uniformity of thickness throughout the Bioflex wrap would rival that of Dr. Shrink
3) Ease of use. Bioflex is compatible with other shrink-products: shrink tape, doors, cordage and heat guns can be used with Bioflex to achieve the same end-result
4) The folds. This may be simply personal preference, but I loved that the width-folds open up on the inside of the roll. Competitor’s rolls unfold on the outside of the roll. This small difference made it easier for me to unroll and manipulate, without having to fight through a mess of unruly plastic.
5) The cost. The only drawback that I saw was the cost difference; compared with other shrink-wrap products on the market. We didn’t discuss firm numbers (as Layfield is still working on their pricing and supply chain), but it is estimated that Bioflex will cost 10-15% more for similar sized rolls, compared with comparable products.
6) The Availability. Bioflex isn’t available (yet) via marine chandleries or wholesalers.
7) The Disposal. Layfield has really focused on this as the main driver in entering the market. Here’s how the environment benefits:
Traditional shrink-wrap plastics are folded, separated and collected and sent for recycling. I’m not an expert in this field, but I would guess that the ‘value’ branded shrink-wraps on the market are made from recycled plastic. I’ve heard stories and rumours of some of this plastic being shipped to China for re-manufacturing. I’ve even heard snippets of conversation that suggest that China has recently been refusing to accept some of the North American plastics (shrink-wrap included). The alternative is for plastics to end up in landfills across the country.
Conventional plastics can take hundreds of years to break down, and while this process is happening, they take up valuable landfill space.
Landfills of decades past were heaps of trash, being picked over and moved by man and machinery. More modern waste disposal sites are set-up to allow the gases emanating from decomposing trash to be collected and utilized as a fuel for power generation. This gas is referred to as ‘biogas’.
Bioflex Marine Shrink is designed to increase biogas production, harnessing the potential energy in plastic molecules.
Layfield Geosynthetics has done this in such a way that consumers need not change their habits (ie The same marina/yacht club sorting and disposal that is being done now can and will continue – the sorting and breakdown all happens at the waste disposal site).
Layfield’s marketing materials also indicate that their Bioflex wrap is UV stabilized, puncture resistant, easy to patch, and won’t degrade on the shelf.
Here’s a small disclaimer from Layfield:
*BioFlex™ has been shown to produce biogases 23 times faster than conventional plastic in the ideal conditions of an anerobic digestor landfill over the course of 2.13 years, using the ASTM D5511-12 test. When disposed of in a landfill with modern biogas capture technologies, this energy can be harnessed as a source of renewable energy. Such a facility may not exist in your area.
All in all a win-win: A product that is more environmentally conscious than competitors’ products, with the same ease-of-use – allowing contractors and boaters to continue operating in the same manner as traditional methods.
Keep your eyes peeled in 2020 for Bioflex at a boat yard near you.
Andrew McDonald is the owner of Lakeside Marine Services – a boat repair/maintenance firm based in Toronto. Andrew has worked in the marine industry for 12 years and is a graduate of the Georgian College ‘Mechanical Techniques – Marine Engine Mechanic’ program.
Questions or comments for Andrew? Email him directly via: askandrew@lakesidemarineservices.ca