Ask Andrew: Acrylic and Ceramic Gelcoat Restorers – Miracle Cure or Stumpwater?
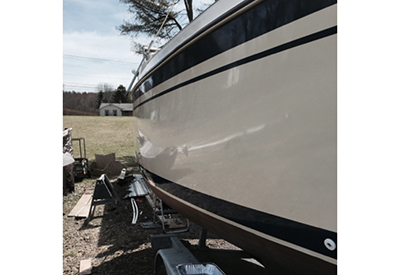
Nov 11, 2021
a fresh acrylic coating
Fibreglass boats take a lot of maintenance. Their appeal, half a century ago was their ‘maintenance free’ nature when compared with wooden boats. Add in the ability to mass-produce, and the low coast of manufacturing made fiberglass and easy choice.
A revolutionary line of products aims to take fiberglass to the next level. But do gelcoat restorers live up to the hype?
oxidized and worn gelcoat on a boat’s hull
First, lets take a look at what gelcoat is, and the standard maintenance regimen that a fiberglass boat owner takes on each year:
A fiberglass boat is made up of a sandwich of layers – a core material surrounded by layers of woven, mat or strand hair-thin glass fibres that are soaked in a resin. The resin cures when a catalyst is added and after curing the glass-fibre infused layers become hard without being brittle, strong in each axis, and pound-for-pound exceeds the strength of comparable products available for boat building.
A great combination. But not at all pretty. And not terrible functional -the pretty and functional part comes from the gelcoat.
Gelcoat is in the fiberglass family: it’s a base coat (similar in consistency to paint), to which a catalyst is added to make it cure. Gelcoat can be brushed or rolled on, or thinned and sprayed using a paint gun. Gelcoat is a number of millimeters thick, on the surface of the fiberglass, and can be sanded and polished to a bright shine. Pigments can be added to a white base to create almost any colour. The hull of a fiberglass boat is typically left smooth and shiny, where the decks are molded to create a combination of smooth and non-skid areas. Manufacturers have combined curvature, symmetry, styling and colour permutations in innumerable ways.
Gelcoat is porous – it collects dirt and oxidation that dulls and changes the shine. UV exposure can also change the colour over time. Gelcoat requires maintenance in the form of polishing and waxing (and sometimes filling, sanding and fairing). Polish is a light abrasive (from 1000-2000grit) that can be applied by hand or using an orbital machine – it removes the dirt and oxidation through a very fine sanding process. The porous gelcoat is then coated in a liquid wax (often applied by hand or machine buffer) that fills the pores and leaves a smooth shine.
The polishing and waxing process is a lot of work. It can take a few hours to a day to complete the polish and wax on a boat’s hull – or if you want to hire a contractor to do the work for you, it can cost from $15-$25/ft of boat length. A 30 ft boat could cost from $450 – $750 for the hull alone. Polishing the deck is an added cost.
a worn acrylic coating
Beyond the cost in dollars, is the toll that this process takes on the hull: each time the hull is polished a very fine layer of the gelcoat is removed through the abrasive action of polishing. Over the course of 30 years, the gelcoat wears thin, and the fibrelgass can be seen peeking though.
In short, boaters are after a clean, shiny gelcoat surface, without the headache and effort of the maintenance. Needless to say, there is a wide open market for products and services to make this process easier and cheaper with the same or similar results. Enter the acrylic and ceramic gelcoat restorers. There are a number of brands readily available: Poli Glow, Vertglass, NuGlass2 (NewGlass2), Glidecoat, Presto Gelcoat Rejuvenator, Glass Cote, etc.
They each work in a similar way: prep the gelcoat surface and apply a number of coats (5-8 is recommended) of the restorer product. These restorers are designed to bond to the underlying gelcoat, filling its pores and leaving a smooth and shiny surface. No polishing or waxing required. Annual recoats are recommended (but skipping a year or two is possible without major adverse effects).
It sounds like the perfect solution, however:
The devil is in the details – applying the products according to the directions is imperative (including surface prep): not following the method of surface prep and application described is a recipe for a wavy or streaked surface, with any imperfections permanently locked in place.
No touchbacks: once it’s done, it’s done. A hardened, multi-layered acrylic or ceramic surface can’t easily (or cheaply) be undone, fixed or touched-up.
You’re committed: Common marine cleaners can’t be used on some of the restored surfaces without adverse effects. Each brand produces its own line of cleaners, preparation products and removers that aren’t compatible with each other, or other cleaners you may already have on board.
One of the other drawbacks that may not be considered at first is the long-term maintenance of your boat. Dings, nicks, accidents, cracks, etc will happen over time. A repair to straight gelcoat isn’t terribly difficult. But how does one go about repairing a hull, that’s been coated with 5-8 layers of acrylic or ceramic, leaving the completed repair uniform with the rest of the hull? The repair has now become significantly more costly and time-consuming.
I’ll have to admit my bias. But I feel with good reason; I’ve only ever seen an acrylic or ceramic hull job that has been botched. I’ve been called on-site a number of times when owners have asked to have the product completely removed. In each case, I’ve arrived to see the hull surface patchy, peeled and spotty. After exposure to weather, rubbing against lines, docks and fenders, the surface has looked more like dinged-up plastic rather than the shiny smooth hull that was advertised.
I’m sure that there are some success stories (and I’d love to be proven wrong over time) – the owners that I’ve met who have chosen to use ceramic and acrylic restorers do so because the underlying gelcoat was in such dreadful shape that this was their last option before investing in a gelcoat paint job. Until I’m proven wrong, I’m going to continue to recommend gelcoat being used to fix gelcoat, rather than applying a hard sealer on the surface.
Andrew McDonald is the owner of Lakeside Marine Services – a boat repair/maintenance firm based in Toronto. Andrew has worked in the marine industry for 12 years and is a graduate of the Georgian College ‘Mechanical Techniques – Marine Engine Mechanic’ program.
Questions or comments for Andrew? Email him directly via: askandrew@lakesidemarineservices.ca