Modernizing Tradition at Rossiter Boats
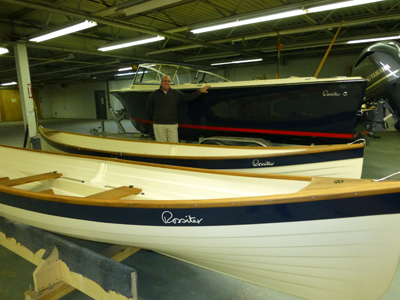
By Kate Fincham
Scott Hanson stands proudly by a new Rossiter 23 Day Boat with Loudon rowboats in the foreground.
Walking in to the small showroom at the Rossiter Boat factory, the company values and evolution of tradition become immediately apparent;it is a small but thriving manufacturer that truly cares about exceptional quality and customer relationships. A wall of framed emails and letters from delighted customers line the walls like children’s photographic timelines in a proud parent’s home, which Captain John Armstrong and I peruse in between sipping mugs of hot tea offered by the amiable Trisha and petting the affectionate office dog belonging to the company’s owner, Scott Hanson. We soon discover what is only further enhanced by the ensuing two-hour tour: the company is heavily invested in its modest beginnings and is an organization where quality service comes with a place in the extended Rossiter family.
The history of Rossiter Boats is one that combines passion, fostering of tradition, and an eye towards the future. It all started 40 years ago with 19-year-old George Rossiter repairing the wooden canoe of a fellow cottager on Go Home Bay. As word spread about his woodworking abilities, George was continually sought afterto undertake various restorations of wooden crafts. After completing a marine engineering degree to further his knowledge and gain a deeper understanding of composite materials,George Rossiter began the transition from restorations to boat building.Expanding from the classic all-wooden crafts that he had been restoring, he created a traditional style of rowboat that was composed of a fiberglass hull and handcrafted woodwork finishing. This same style, with slight changes and additions for improvement, still remains Rossiter’sbest-selling rowboat- the Loudon.
In the infancy of his boat building days, George would locally sub-contract the construction of fiberglass hulls before doing all of the wood finishinghimself. Unable to get sufficient hulls at the pace and quality he desired, he established his own fiberglass shop in a small three-car garage in Meaford, Ontario, with the help of two craftsmen from Owen Sound, Ontario. Around this time the first Rossiter powerboat, the Rossiter 14’, was created.
Needing to significantly reduce his workload, George began looking for someone to take over the business that he had lovingly created and grown for 30 years. The opportunity presented itself at a Christmas cocktail party in 2006 when George ran in to Scott Hanson, whom he had met at the Collingwood Maritime Academy a few years before. At that time,Scott was a marketing professional working in Toronto, but had a degree in boat building and yacht design and shared George’s passion. George proposed an extreme departure from life in the city, and after some contemplation, Scott accepted the offer to purchase the company.
Since that time, Scott has used his skills and enthusiasm to grow the business from a 3,000 square foot garage to a 92,000 square foot custom-outfitted plant in Markdale, Ontario. Demand and productionhas increased tenfold. He laments that he no longer physically participates in the boat building process as he used to 10 years ago, but is happy to be the driving force behind maintaining and growing the company. “The guys in the plant said to me ‘you know what Scott? I think your time’s going to be better spent going out marketing the company even though you love working with your hands and building boats. Let us build boats. You can create full-time instead of seasonal jobs for us. You should go push some paper again.’ So I did.”The expansionof production means that Scott is now able to employ 30 staff withsecure,year-round jobs. While some of the team joined with a great deal of experience in the area of marine construction, quite a few are local with little to no experience in boat building and, similarly to Scott, come from occupationally diverse backgrounds. Many have been hired for their transferable skills and aptitude. For example, Mike, the plant supervisor, worked for years at the distribution centre of Canadian Tire before coming out of retirement to work full-time with Rossiter. The evidence of his organizational skills and aptitude is ubiquitous around the plant- everything down to brooms has a specific place and inventory is meticulously accounted for. He and every employee is a vital cog in the boat-building process, and are collectively a team that Scott views as a family.
Ourfactory tour began with Richard, the carpenter, at the last step of the production process, in the bright sunlit woodshop where all of the wood finishing for the boats is meticulously handcrafted. Richardwas hard at work creating a teak table and custom swim platform for one of the 23-foot powerboats. Richard is a highly skilled and experienced woodworker and boat builder, something that is clearly evident in the incredibly crafted pieces we saw throughout our time at the factory. Perpetually looking towards the future and the growth of the company, Richard also has an apprentice, Aiden, who recently completed a college degree in woodworking and has been brought on to learn the intricacies of boatbuilding and finishing.
An early fiberglass Rossiter in the foreground and the latest Loudon beyond.
Heading into the cavernous depths of the factory reveals an impressively purpose-constructed space with several ventilated enclosed booths for gel coating, laminating and preparing the hulls, large open spaces for laying out the boats to be wired and fitted, and a room for storing and inventorying the upholstery. Unlike large-scale boat production facilities, there is no robotic automation of the building process. High-tech materials are used in the composition, but all of the construction is done by hand to ensure quality and a dedication to the craftsmanship that is deeply embedded in the DNA of Rossiter.
Richard is a highly skilled woodworker and boat builder and with his apprentice, Aiden runs the wood shop.
The construction process begins with the mold (each one capable of producing over 600 hulls) being waxed and the colourgelcoat applied. A barrier layer and a skin coat of resin mixed with chopped fibresis sprayed onto this, which enables proper adhesion of the stitched mat materials. Multiple layers of durablecloth with a strategically oriented weave pattern is laid onto this foundation and, using grooved aluminum rollers, is saturated and affixed(during our tour, this was executed by Jonnie, a veteran boat builder who has been with Rossiter for eight years, and his apprentice). Moisture-resistant structural foams of various densities and properties are strategically placed in the hull and superstructure to provide a strong, durable laminate. Once the stringer grid has been attached and the parts have dried, they are carefully inspected and individually weighed to ensure quality. A part that is underweight may be indicative of an incorrect ratio of glass to resin or insufficient coating, whereas one that is too heavy might compromise the durability of the hulls that they aim to build, thereby reducing fuel efficiency and overall performance of the boat over its lifetime.
The new facility in Markdale, Ontario accommodates top quality molds and glass work.
At this point, the process for the rowboats and powerboats diverges, with the nine types of rowboats they build here going on to be finished and the woodwork applied by Richard. Using a similar hull to the powerboats has made the rowboats slightly different than the original models created by George Rossiter in terms of lighter and more durable hulls, but the functionality and aesthetic have remained the same.
The powerboat hulls in turn are moved to the next portion of the plant where the stringer grid is mated to the hull andthe fuel tank and flotation foam is added, after which the liner is bonded to the stringer grid and hull to create a single solidstructure. After this, the details are taken care of -the marine-grade electrical wiring and plumbing (for the Classic Day Boat and 23’ and 20’ models) is installed, collapsible deck cleats with self-contained drainage systems are put in, and custom-made aluminum fuel tanks and windshields are affixed. Teak decking is laid as necessary, the rope or stainless rub-rails put on, lighting installed, and all of the finishing touches complete. Wherever possible, Scott tries to use locally sourced services and parts with the upholstery contracted locally, the covers and Biminis made by third generation seamstresses in Parry Sound, and handmade oars coming from Western Canada. The resins, glass cloth, hardware, plumbing, and electrical components are all sourced from the United States.
When all of the processes are complete, typically four to six weeks from the inception of the process, the boat is sent to Sean for quality control. The rigorous tests that the boats are put through are meticulously completed using a 6-16 page checklist, and can sometimes take as long as four days to complete for a single boat. “The best part about semi-custom boats,” Sean happily tells us “is that there is something new every time.”
Even with the 60 rowboats and 200plus powerboats they are currently producing out of this factory on a yearly basis, each and every boat receives careful attention to detail and customizations based on customer requests. Scott estimates that the infrastructure of the facility could accommodate an increase that is three to four times what they currently produce while still maintaining the dedication to quality and craftsmanship that the business was founded on. “We’re a very different company now in terms of size, but we’re no different in terms of George’s commitment to quality, performance, and building boats one at a time.” This historic dedication shows. Each boat- very much a unique vessel at the intersection of customer input and handcrafted skill- is a product of the extended Rossiter family.
They are pieces of art, testaments to craftsmanship, and a new symbol of Canadian boatbuilding.