Around the Boatyards – Coastal Craft
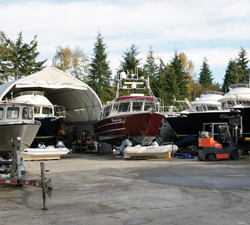
From its aluminum workboat roots, Coastal Craft is emerging as a leading builder of high-performance semi-custom yachts, with an emphasis on innovation.
From its modest start in 1996 as a builder of welded aluminum crew boats, Coastal Craft has emerged as an industry leader in high-performance, high-tech semi-custom yachts. There are probably more than a dozen manufacturers of aluminum workboats on the British Columbia coast – but Coastal Craft has moved far beyond that original niche.
The Coastal Craft team once comprised just founder Jeff Rhodes and three employees – but now numbers 50 and growing. Rhodes is quick to explain that he did not set out with a grand vision to become a manufacturer of premium yachts. Instead, he grew into the role by listening carefully to his customers, then building what they wanted.
“I came from the towboat side of the marine business, and started building welded aluminum work and crew boats,” Rhodes explains. “After a couple of years, a customer wanted the warmth and charm of a real wood interior. I said we’d build him one. Then I had to learn how. And that led us into building yachts, not workboats.”
Innovation
Learning is a continuous process at Coastal Craft and it never really stops. CY West had a recent tour of their growing manufacturing plant in Gibsons, a town of 4,200 on B.C.’s Sunshine Coast. With an 18-month backlog of orders, the plant is full of high-tech production equipment and busy workers, components and parts being assembled, and boats being finished. Two of Coastal Craft’s newest 56-footers were under construction, a 45-footer was ready for the paint shop, and several customers’ boats were in the yard awaiting system upgrades. The largest Coastal Craft to date, a 74-footer, is on the design table and it’s gorgeous.
While the company offers a full product line, more recently it has concentrated on the larger sizes that today’s customer is asking for, the 40, 45, 56 and soon the 74. Thirty and 34-foot models are also available but it is the larger boats that are selling these days.
Coastal Craft has built an enviable reputation throughout the industry for innovation in construction and performance. The company was one of the first aluminum boatbuilders to fit Volvo Penta Inboard Performance System (IPS) units into a new design. That early step got a lot of attention from Volvo engineers and the partnership has flourished, while Coastal Craft’s success with IPS is becoming recognized worldwide.
IPS mates high-performance Volvo Penta common-rail six-cylinder diesels to steerable drive pods with forward-facing, counter-rotating propellers. Operating in clean water, the IPS delivers high cruise speeds and excellent low-speed maneuverability. IPS is now the default propulsion system for the entire Coastal Craft line.
High-speed cruise is just that – 30 to 35 knots standard at a reasonable fuel burn. The fuel consumption curve is almost linear – close to one nautical mile per gallon at almost any speed using ISP600 power packages in the 40 and 45-footers. These are planing hulls, with clean hull forms and strong construction that make these speeds routine.
Finger-tip maneuverability while docking comes from a simple joystick control – just tip the stick in the intended direction of travel and the boat moves that way. Thrusters, bow or stern, are not necessary. The system works so easily and directly that boating couples report that both partners can dock with confidence. That alone – to say nothing of domestic harmony aboard – could justify the investment.
Quality and Performance
This kind of innovation is matched elsewhere on the boats, as well as in the plant. Coastal Craft specifies only LEDs for interior lighting, taking advantage of their low current draw. Helm chairs in the wheelhouse and on the flying bridge are Stidd, while Diamond Sea Glaze supplies the windows throughout.
“It’s not that these are just well-known brands,” says Rhodes. “They are well-known for the same reason that we specify them – they provide us with the quality and performance that our customers expect.”
Gensets are Northern Lights or Fischer-Panda; the latter have a smaller footprint that leaves room for other accessories. US Watermakers are standard, as are Miele washers and dryers on larger models. All interior wiring is high-quality marine-grade from Vertex.
We saw a 56-footer being fitted out with a five-area in-floor heating system, complete with plenums and controls in a high-quality installation more usually found in upscale homes.
Component choice requires a never-ending search for quality and performance, says Rhodes.
“Not many boat builders are prepared to invest in the R&D necessary to be on top of technology, but we are.”
This is reflected in the boats’ electrical systems, too. Twenty-four-volt systems are now standard, saving weight and cost of wiring. An Eplex low-voltage control system is completely wired throughout; it controls all lighting and other electrical systems – genset, watermaker, heaters, air conditioners – from keysets in the wheelhouse, salon and master stateroom. Surprisingly, lithium-ion cells are now standard in house batteries.
“No other battery gives us the performance we want. It’s worth the premium price to get a battery system where we can use the entire capacity of the cells, and it will fully recharge in minutes, not hours” explains Rhodes. “Boaters want to minimize the amount the generator is needed and we’re down to less than a half-hour, twice a day on average, to keep fully charged.”
In the galley Coastal Craft installs Sub-Zero refrigeration and the latest magnetic induction coil cooktops. These will heat only a metal container, not a hand, so safety and performance is packed inside, too. An impressive integrated electronics package is fitted on the bridge and at the main helm station.
High-Tech Plant
As one might expect, Coastal Craft builds its advanced boats in a similarly modern and well-equipped plant. Though crowded with production now, it’s as up to date as any factory we have visited.
The sprawling facility is located off the main highway in an industrial area of Gibsons. Covering 20,000 square feet, it’s divided into five main areas: hull fabrication (mostly welding); wood shop (where interior cabinetry is cut and pre-assembled); paint shop; (a few steps away); and, mechanical preparation area. Offices are located on the second floor. Immediately next door is a new, semi-permanent tent that houses the final fitting-out area for the 56 and the 74.
Bustling with activity and workers everywhere, the entire facility was well organized, neat and clean. There is a general air of “busy-ness” and a quick pace to everything; spirits are obviously high. Employees are clearly proud of their work and were quick to show it to us.
Nowhere was this more evident than in the carpentry shop. About $500,000 has been invested recently in the latest computer numerical-controlled (CNC) woodworking equipment. We watched as a 4’ by 8’ sheet of marine-grade okoume plywood was loaded on the flat bed of the CNC cutter. The layout and design of the side table and drawer unit for the 56’s master stateroom had just been downloaded directly from the design office computer-aided design (CAD) system.
After a quick adjustment, the CNC unit proceeded to cut rabbets and mortises, and drill the cross-holes. The CNC operator then flipped the sheet over and the machine cut all the rest of the components. Waste was minimal and the resulting pile of pieces was neatly stacked and labeled for correct assembly. Quality cabinet-making has never looked so easy – this process saves countless hours and ensures a perfect fit.
Rhodes is particularly proud of his team’s consistency of build. Matching the strength of welded aluminum and the precision of CAD designs with precise assembly creates a boat that retains its stiffness, strength and integrity. Ten-year old boats in the shop for upgrades still show precision fit of interior components with no flex or degradation. Our inspection of one 56-footer found remarkable quality of fit and finish even in areas that would remain forever sealed and hidden. Quality of work was evident everywhere we looked.
As part of their progression to producing premium high-performance yachts, Coastal Craft now builds to Transport Canada, US Coast Guard and American Boat and Yacht Council standards.
Performance
We rode on a Coastal Craft 42 fitted with IPS last summer and were astounded with the performance. At well over 30 knots (max is closer to 40 knots for newer models), the deep-vee hull kept the ride soft, dry and flat even in a fair chop. Floating debris is a hazard but Coastal Craft has found that the forward-facing props are not as vulnerable as one might imagine. The company has designed and installed a protective Drive Guard, a small skeg that is precisely sized and sited just ahead of the props to help protect against log hits. However, the operator at the helm still needs to be attentive at speeds of 30-plus knots.
With a growing international sales and dealer network, Coastal Craft is now attracting customers from far afield. The company exhibits models at major boat shows and is always ready to show prospective customers around the factory to demonstrate their build process.
A semi-production shop, Coastal Craft offers standard model configurations but finishes each boat to the customer’s particular needs. This creates a lot of interaction with customers as layouts, specs and equipment are developed or modified. The latest CAD technology makes this process much easier –and produces happy owners.
With a full order book, a growing international customer base, and a reputation for innovation and quality in yacht construction, Coastal Craft is building on its enviable success story.
By Robert Buller