Behind the Scenes at MJM Yachts
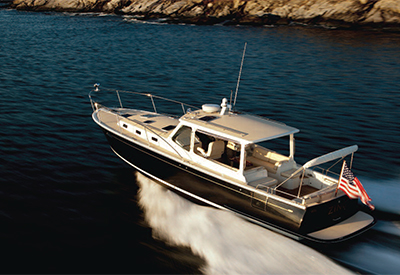
By Kate Fincham
Nestled under an old iron bridge spanning Boston’s Mystic River lies a modern glass and concrete-paneled building, seemingly incongruous with the surrounding 1930s factory structures. This is the new facility of Boston BoatWorks, the exclusive builders of MJM Yachts. The location is an apt metaphor for the incredible yachts produced in this space; MJM combines old principles of boat design with modern techniques and materials to produce extremely light, stable, fuel-efficient yachts.
It was at this facility that Captain John Armstrong and I were invited for a tour on a snowy day in January. We were greeted by Scott Smith, the co-founder of BBW and Christopher Hughes, strategic marketing partner at MJM, and led to a bright conference room with a large window overlooking the historic Charlestown Navy Yard. In this auspicious space we were given an enthusiastic briefing on MJM Yachts, from their initial production of the 34z model in 2002 to the current exclusive manufacturing of 40zs and 50zs, before being taken down to the manufacturing facilities.
In the initial portion of our tour with Hughes and Smith we were introduced to MJM’s impressive and unique hull manufacturing process, one which enables them to be extremely durable and lightweight. Firstly, the inner layer of woven isotropic laminate material is saturated with resin before travelling through rollers to remove any excess liquid. This produces a material that is atypically composed of a higher percentage glass to resin ratio, making it much stronger and lighter. This pre-impregnated epoxy material is layered with a one inch thick closed-cell foam core and then with an outer layer of puncture-resistant Kevlar composite. The entire structure is then sealed in a large bag through which resin is pushed, after which the room is transformed into a sort of enormous yacht convection oven, heated to 145°F and left to cure for 24 hours. Compared to the industry-standard chopper gun fiberglass method of manufacturing motor yachts, this is an arduous process that is expensive and labour-intensive, but is one that produces unparalleled durability and lightweight hulls.
A large part of this unique construction method of the MJM hulls Smith attributes to the BoatWorks’ historic involvement in the production of America’s Cup and development class sailboats. With sailing yacht design, a significant component of speed is determined by weight; the lighter the better. With motor yachts, on the other hand, weight comes at a very slight premium; added horsepower is relatively cheap, so hulls can afford to be heavy and bulky. “The difference between a carbon fiber America’s Cup boat and an MJM” Smith joked, “is that if the carbon fiber boat survives the last America’s Cup race, it was probably overbuilt.” The most significant benefit of this reduced-weight hull is fuel economy, allowing for cheaper operating costs and a more environmentally friendly boat capable of travelling long distances. The range of their largest yacht, the 50z, is up to an astounding 1,450nm cruising at 8 knots; at a speed of 35+ knots a Canadian boater could easily take a day trip from Toronto to Kingston and back on a single tank of gas.
While we walked through the preliminary stages of the hull manufacturing process, a half dozen workers were laying resin saturated laminate pieces onto the hull mold. The rest of the factory was a similar hive of activity, with electricians pre-preparing wiring harnesses, builders installing deck hatches and technicians fitting various parts. On a 40z in the final stages of construction, a worker carefully measured the side door (a unique selling feature of MJMs, enabling boaters to step straight out on to the dock), ensuring that the gap around the door was flawlessly uniform and that the levelling was perfect. Meanwhile, Mark Lindsay, Smith’s partner at BBW, carefully inspected the yacht with the production engineer and production manager.
Hughes raved about this team and stated that “Everybody here is as invested in the build as Scott and Mark are”. And indeed, from an outside view it seems like a well-oiled machine. Due to increasing production demand, the workforce at BBW has increased by nearly 50% over the past four years. This growth has not, however, greatly affected manufacturing time of the boats. They build to a pace which ensures that the standards of quality are rigorously preserved. “We could build it in less time if we wanted to, but we don’t” Smith casually remarked. This timing means that they will be building 18 yachts in the factory this year (each one takes about 6 ½ months to complete), with their 200th yacht scheduled for completion in February.
After seeing the meticulous manufacturing process and carefully selected materials, it was apparent that every facet of MJM yachts are of the highest quality and intended to last. But, as Smith noted, these inner workings are not something that the buyers would ever really see; it is insinuated in the proud reputation MJM holds for superior quality boats, and in receiving the highest category certification by the ISO for the 40z and 50z (meaning it is licensed to travel in weather where wind exceeds 40 knots and swells are over 4m). Part of this stability in rough seas comes from the Seakeeper gyro stabilizer, which along with the ease of joystick steering ensures a comfortable trip. These are all part of the draw of the new MJMs; they are incredibly versatile. They can host a solo captain or a party of 20, the climate controlled pilot house allows for trips in colder weather while the large amount of outdoor seating is ideal for fair weather cruising. Wide utility is certainly only one of the many ways MJM yachts set themselves apart from the competitors.
Upon leaving the building facility, Captain John remarked that MJM has the most impressive process and production standards that he has ever seen; high praise for a captain that has toured many boat building factories around the world. Repeatedly turning to designs of the past, MJM are forging into the future with a process that truly revolutionizes yacht building. Regarding the method of construction, Smith boasted, “There’s no one else who does what we do… we’re the only ones. And by the time someone else gets here we’ll be doing something else”.
Photo Captions
Photo 1 – Behind the Scenes at MJM Yachts.
Photo 2 – This is the split mold for the hull of the MJM 50z, getting detailed and polished after the post curing process. To the left is the deck after removal from the mold and prior to having the companionway and hatch openings cut out. The blue is a protective covering removed after final assembly.
Photo 3 – Scott Smith, the President and co-founder of BBW, Boston BoatWorks and Mark Lindsay, Master Boat Builder and co-founder of BBW are the exclusive builders for MJM Yachts.
Photo 4 – The team at Boston BoatWorks are swiftly laying up the pre-impregnated Eglass, Epoxy, and Corecell materials for an interior liner.
Photo 5 – This workstation is where the biaxial and triaxial Eglass is pre-impregnated with epoxy resin before being vacuum bagged and oven post-cured.
Photo 6 – A look at the deck liner with cutouts ready to begin the assembly process and receive its interior features.