Sea Ray Wood Shop – Hallmarks of Quality
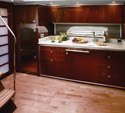
While attending the Miami International Boat Show last February, Rob Noyes, VP of Marketing for Sea Ray Boats made special arrangements for me to tour their new woodworking facility at Merritt Island near Orlando.
I’m a lifelong antique boat fan and refinished my own mahogany runabout a few years ago, so the chance to see the latest, state-of-the-art woodworking facility was an invitation I could not refuse.
I know Sea Ray yachts well and appreciate how much custom cabinetry goes into even the smaller models. I had visions of men with stacks of cherry wood, teak and mahogany nearby, working at modern tables, carefully fitting pieces together and shipping the finished cabinets, trim and doors to the plants where the boat were being fibreglassed.
Plainly, things have changed!
I met Jim Anderson at the plant office and he set me up with safety glasses and equipment so I could enter the plant. No scent of wood greeted me; no clouds of sanding dust covered the floor – or anything else for that matter!
This was the brightest, cleanest and most dust-free plant I had ever been in! The facility is all about perfection and for that, you need the most precise tolerances and most perfect finish. If you think about it, any part that does not fit tight and rock solid, will “work” with the stresses and impacts of waves and winds.
Anything that “works” or moves will eventually work loose. If you think about it, any place on the wood that does not have a thick, protective finish risks water intrusion that can cause spreading degradation of the finish. The more precise the construction and the better the finish, the stronger and more lasting the cabinetry will be. For furniture, life on a boat is a lot different from life in your dining room!
Not fully realizing how far out of date my thinking was, Jim Anderson first explained to me that it all starts with the best possible panels. I quickly learned that while solid wood sounds good for your home, an engineered panel of extremely precise tolerances was best in a marine application. Many layers of thin veneers bonded with waterproof glues are strong, resilient and yet will not move with the extreme changes in heat and humidity that all boats experience.
Sea Ray’s Sport Yachts currently use a cherry wood veneer for their interiors. (To learn more about why cherry wood and what level of precision is needed, see the sidebar about Greenline Forest Products). These come to Sea Ray’s Merritt Island woodworking plant as 4′ x 8′ panels supplied by Greenline Forest Products with facilities in the Greater Toronto Area and Beaufort, South Carolina. We shared a laugh that I had traveled from Toronto to Florida to see wood from Toronto!
Specifically, Greenline actually makes the panels to Sea Ray’s specific tolerances. They use a Russian birch core. The birch can be farmed in a sustainable way and Jim Anderson explained that this wood is a high-end product that stays stable, holds screws well and stays flat. The weight of these panels is somewhat less important than their structural properties.
At Greenline, the panels are measured for precise thickness and tolerances and then, within hours of being checked and measured, American cherry wood veneer faces in book-matched grains are applied in presses. They use different thicknesses of veneers for different applications within the yachts. They have both one-sided and two-sided sheets as well as sheets in both short and long grain.
Jim took me through the process, one step at a time. The freshly unwrapped panel is checked and then up to 15 sheets at a time can go onto the enormous computer-driven router. Vacuums holds the panels down to keep them very flat and the panels are cut with repeatable precision to the thousandths of an inch. Then, they mark each piece for edge banding and each one gets a process code label to identify the part. It travels along from there.
Cardboard is used to protect the cherry wood from darkening during handling due to ambient light exposure. The marks for banding are applied using chalk that sands and vacuums off easily.
They first band the inside openings with a special machine and a very experienced operator. The adhesive is a hot melt glue applied at a very high temperature. Later this goes through the ultraviolet finisher along with solvent which results in a high bond glue that will not come off.
The panels then go to “white wood” sanding. Some panels are built with the veneer grain running lengthwise while other parts need it as cross grain.
After computer routing and sanding, the panel is ready to enter the roll coating line. I was right at home here because it looks very much like a huge printing press with many stations, only it handles wood sheets instead of paper.
The panel is carefully fed into the roll coating line and, just like a printing press, applies many colours. This goes through many steps, starting by vacuuming and preparing the panel to receive a special type of filler to fill the wood grain. The second step applies sealers that protect the wood and prepare it for the topcoat.
In one pass, the panel can be finished in a semi-gloss while a second pass is needed to apply a high gloss. Within this huge and very expensive machine, rollers apply stain and brush it into the grain before the topcoat goes on. Sea Ray is very particular about the stain colour and Greenline has to supply exactly the right grain textures through their book-matching process to enable Sea Ray to reach the quality level they specify.
Perhaps the most amazing part of the process is that as well as heat, ultraviolet light is used to catalyze the finish. Ultraviolet initiates the photo activator in the stain and the coating ends up very glossy and flat as well as thick and very resilient, all in a matter of minutes! Ultraviolet inhibitors in the finish also protect it from the sun in years to come.
For the highest gloss, the panel makes another pass through a different coating process that also adds a fine mist spray.
Both electronic inspection tools and the craftsman’s experienced eye are needed to spot any dust particles or imperfections that may have hit the finish. These are buffed out to perfection before the panel can continue.
Completed sheets get a peel-coat for protection before shipping to the plant. Finally, the finished parts go to the factory wood shop for installation on the same assembly line as the new Sea Ray yacht, minimizing handling and the risk of damage.
The cabinets are all made at the Sea Ray assembly plants from the precision parts created at Merritt Island. I never actually saw a finished cabinet!
But, that doesn’t affect the pride that Jim Anderson and the other craftsmen (and women) take from their work at Merritt Island. Their cabinet materials are a critically important hallmark of Sea Ray quality…but don’t take their word for it, read the sidebar.
SIDEBAR:
Greenline Forest Products
Canadian Yachting traveled to Greenline Forest Products at their Toronto area facility and we interviewed Randy Mikals, President of the Greenline operation. He told us, “We supply many boat companies and Sea Ray is extremely demanding – their quality is second to none. The specs for their cherry wood veneer is in an extremely tight range.”
Randy continued, “We start with the highest quality multi-ply marine core that is available – up to 12 plies in some pieces. We travel the world for our woods and I know of no better quality.” Randy went on to talk about how the cherry wood veneer is sourced from the Pacific West Coast and Pennsylvania, from managed forests. The cherry wood is an excellent choice for marine use and gives a warm but lighter environment than mahogany or some other woods. He also explained how the cores are veneered only hours after careful measurement to ensure the precision Sea Ray requires.
It turns out that for the roll coat line at Merritt Island could not achieve the results they do without those tolerances. And, they do measure the gloss with a special tool that rates flatness. The process is called “wave sine” – Sea Ray requires a minimum reading of 10 [but they typically run 3 to 5] which indicates the panel flatness. Many good competitors use a 15 to 22 wave sine.
Elegantly finished wood is the trend for high-end boats. The buyer demands real wood and the days of Formica or phony finishes are gone.